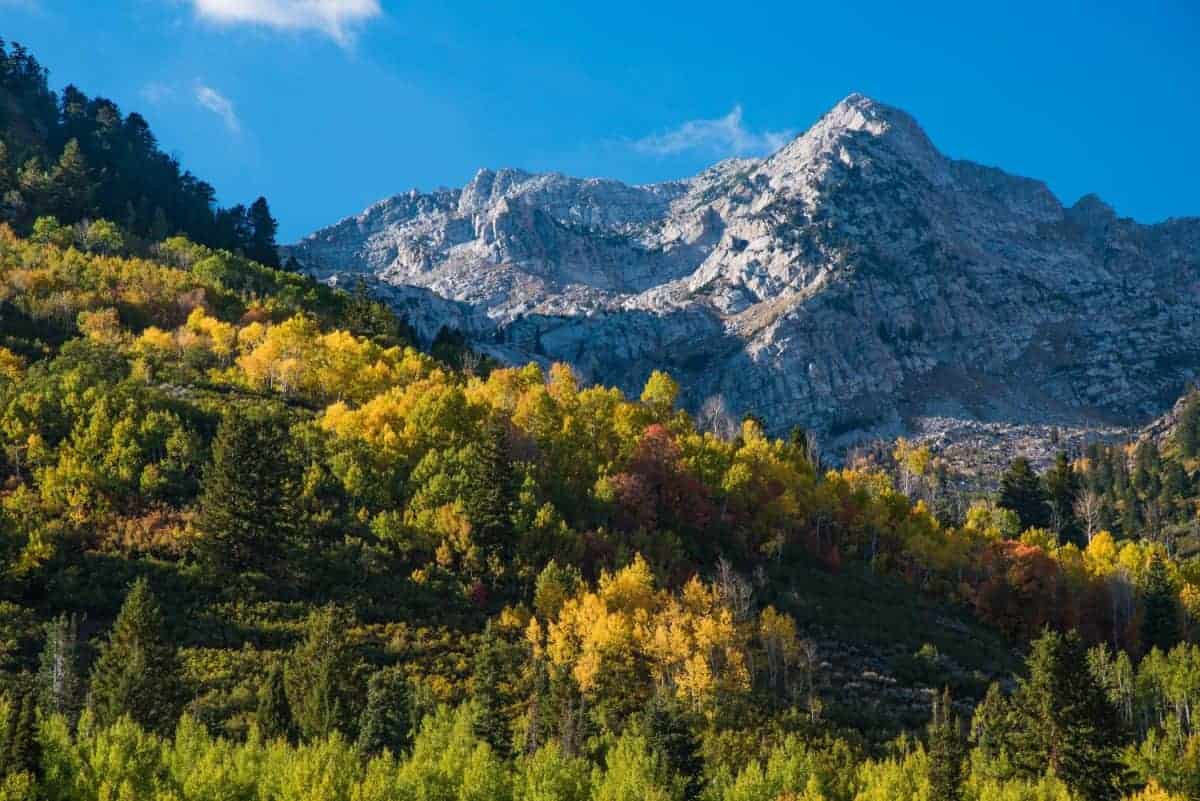
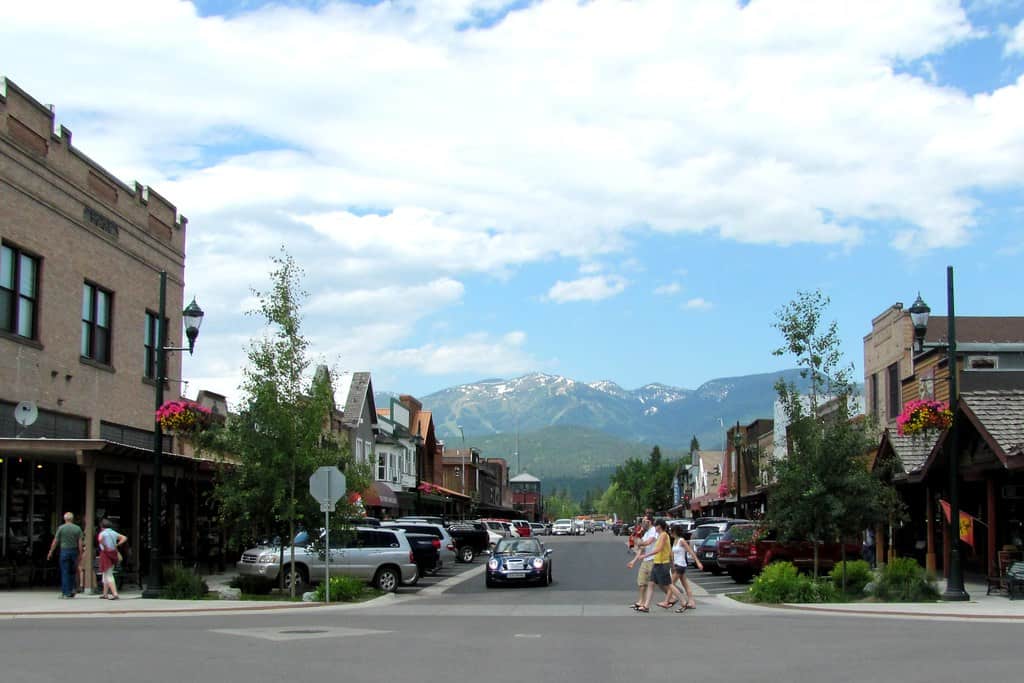
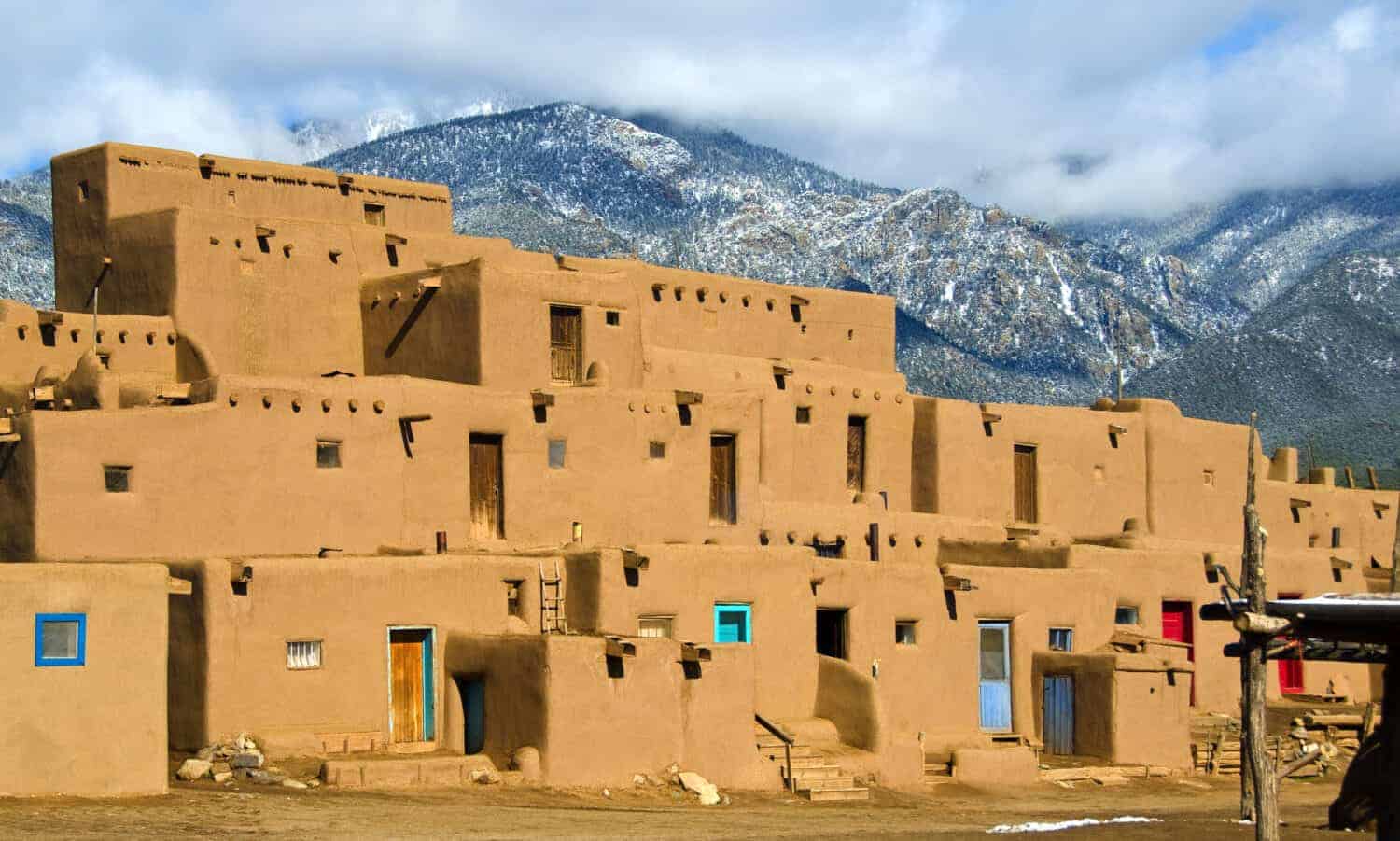
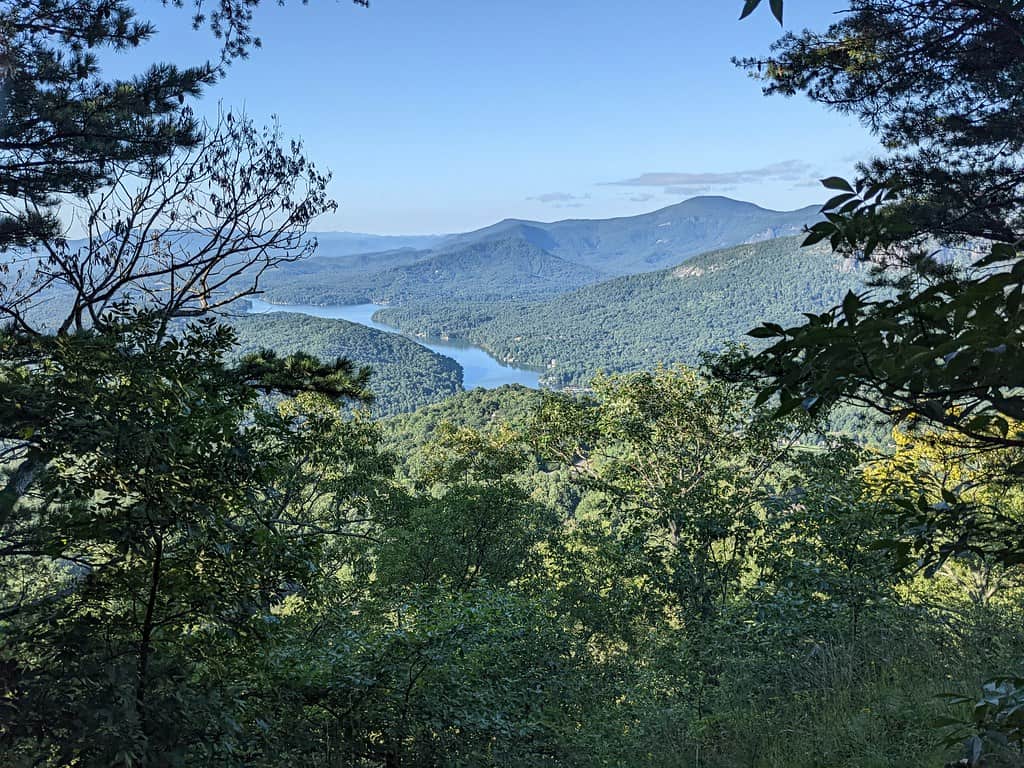
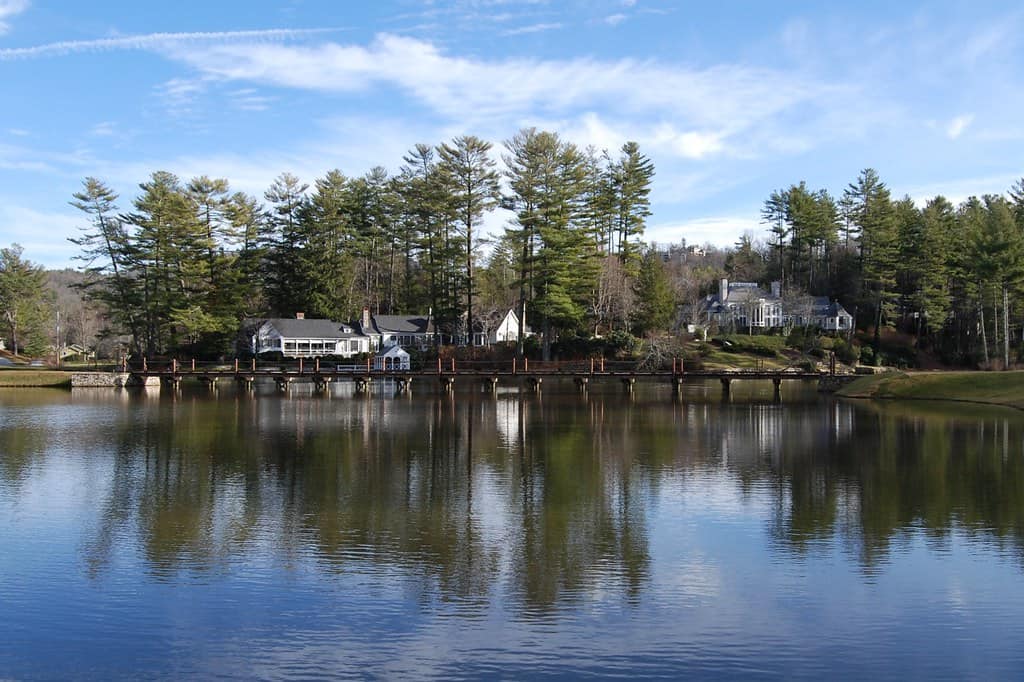
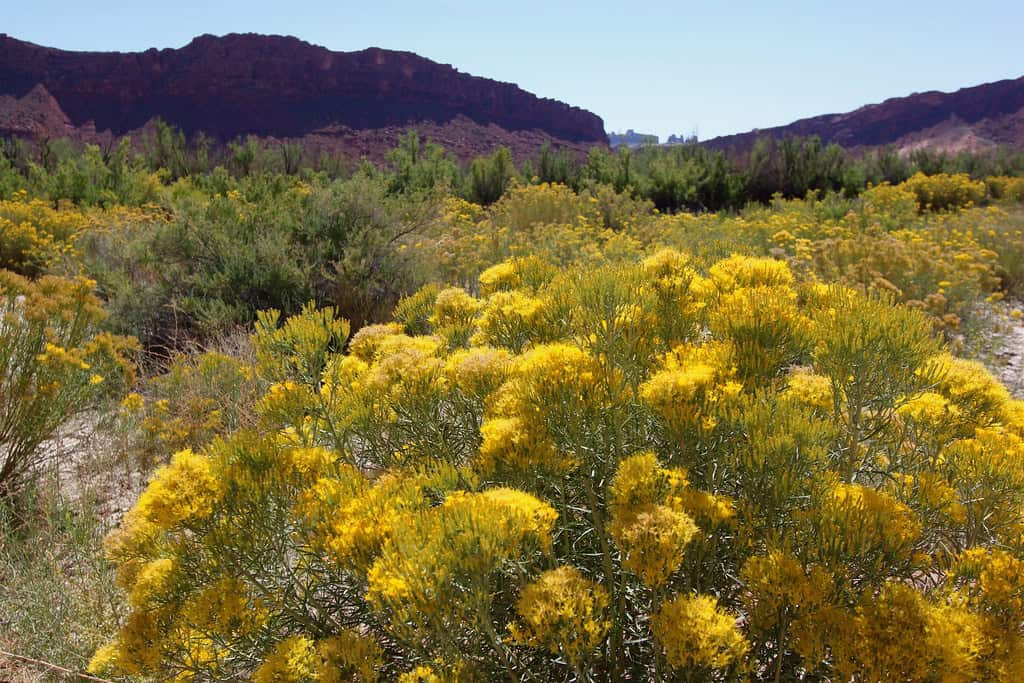

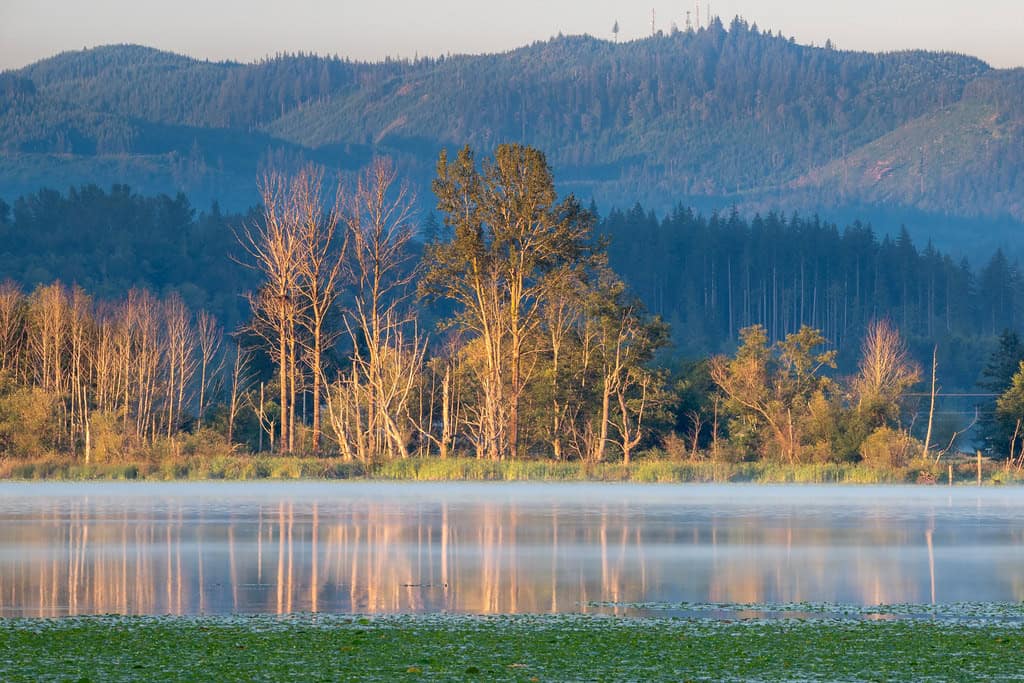
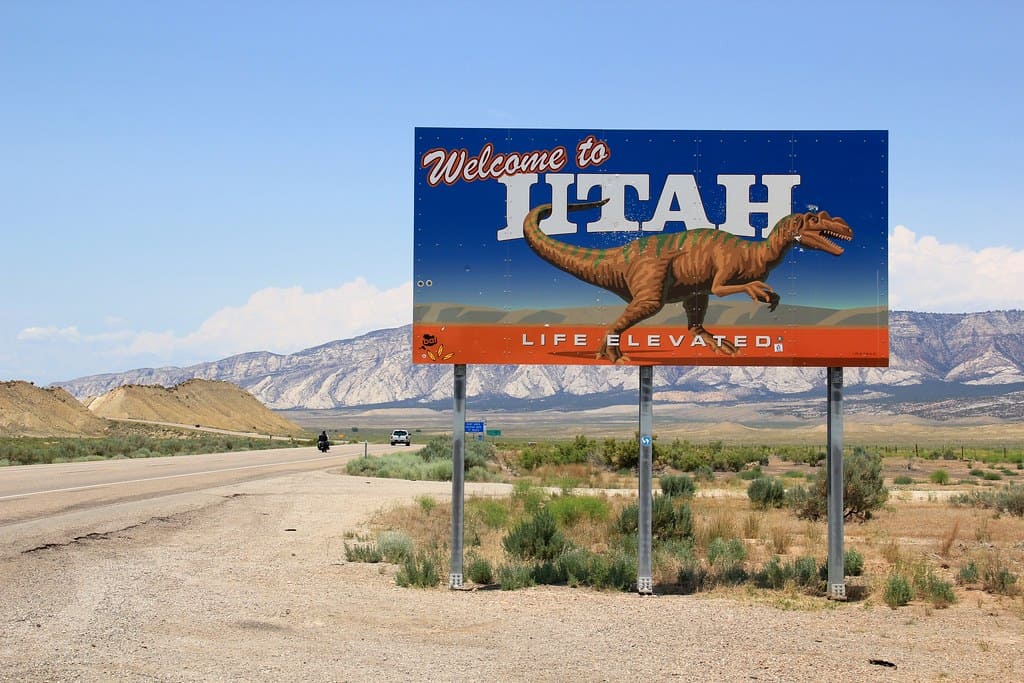
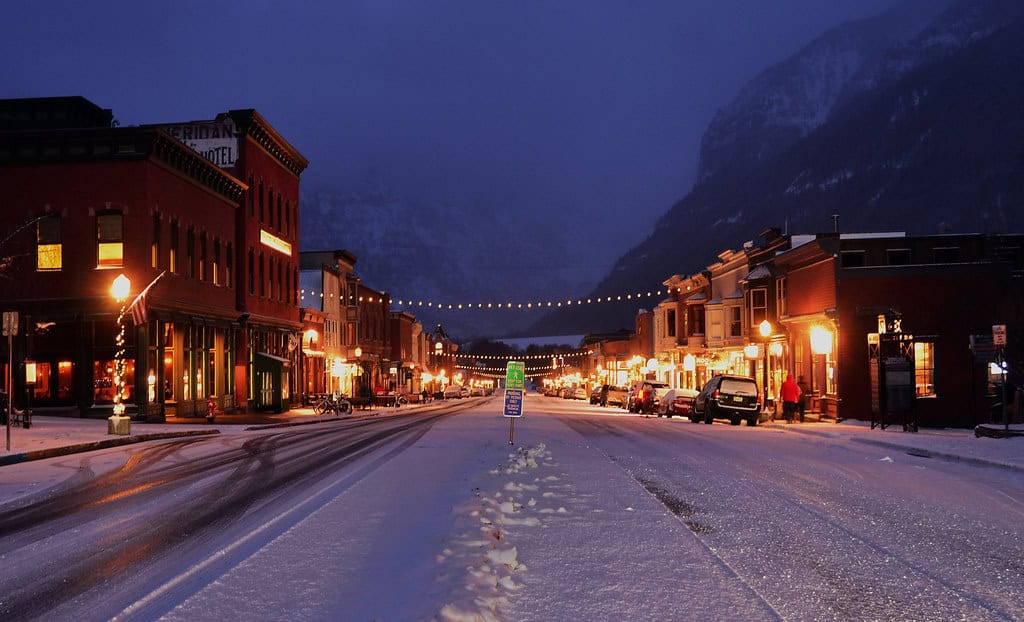
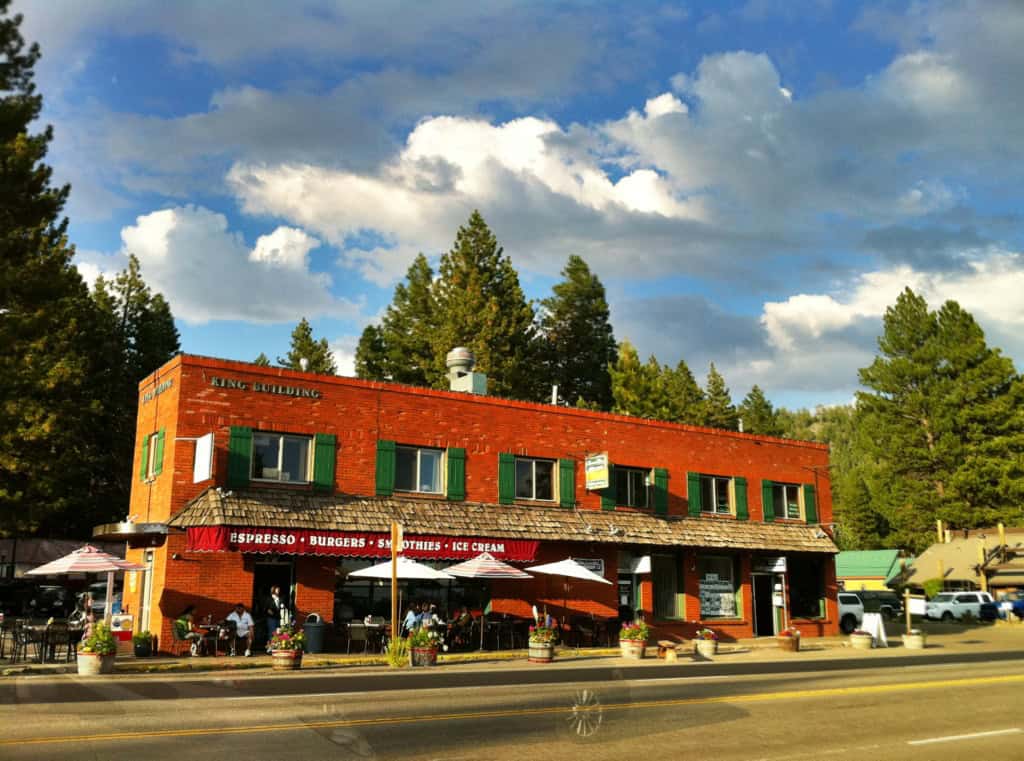
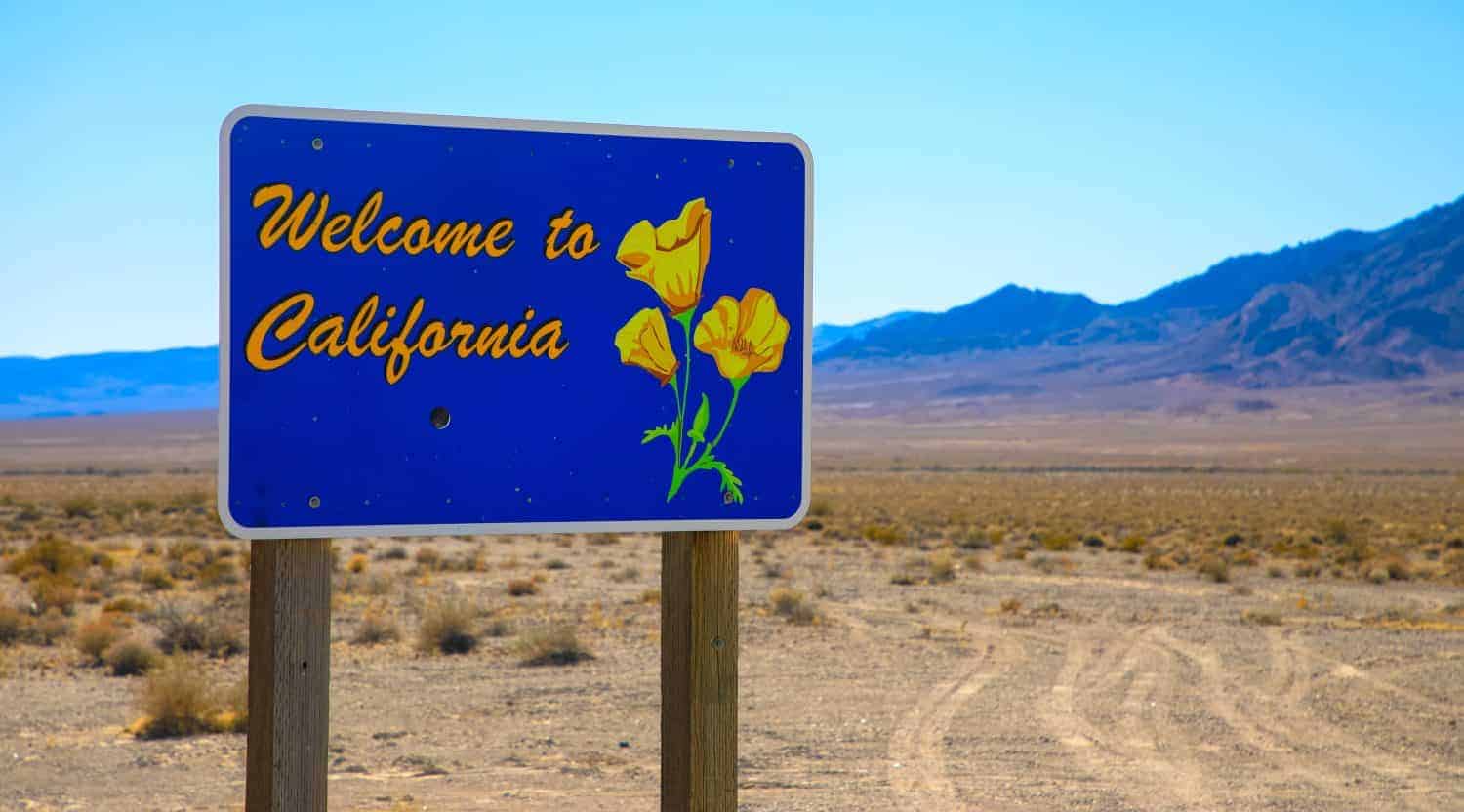
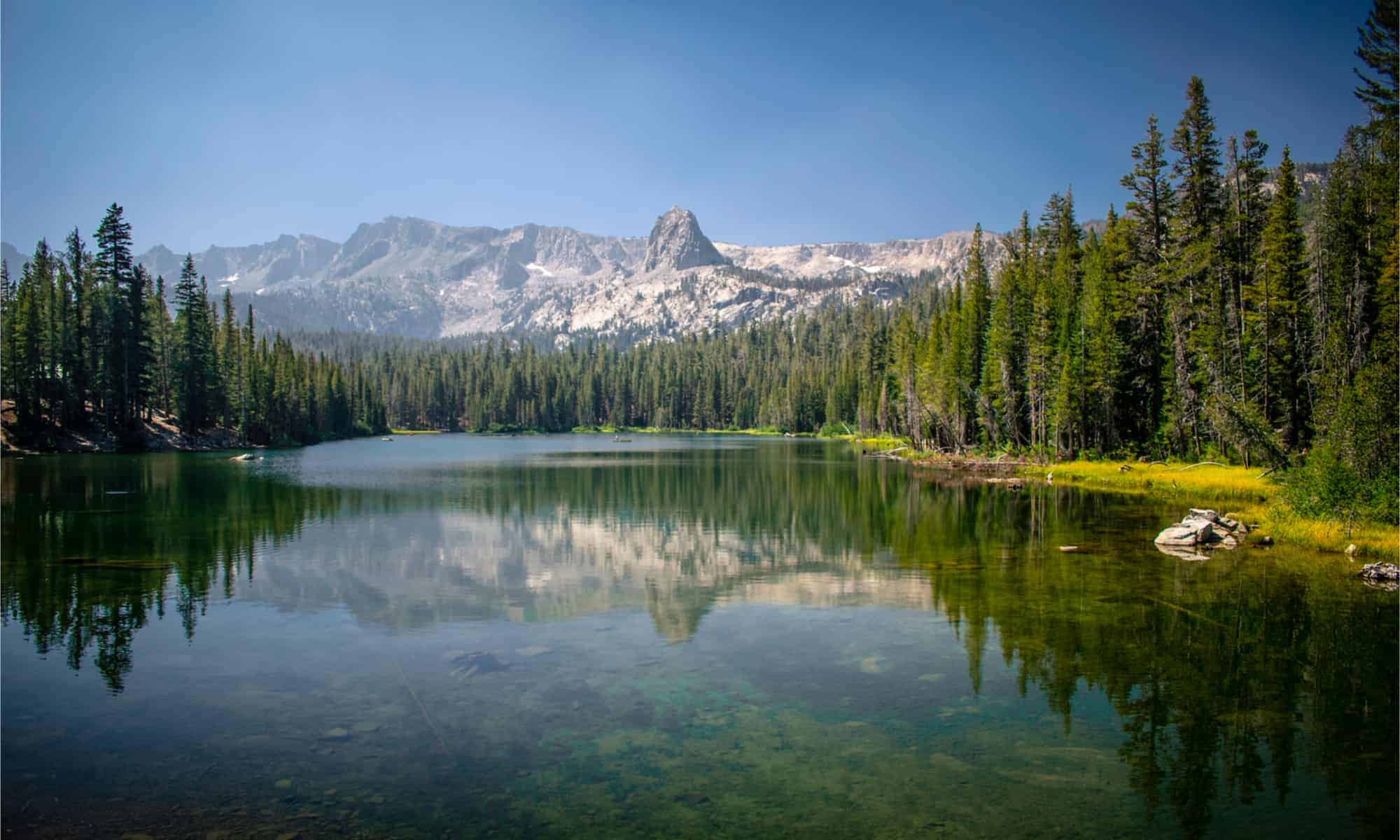
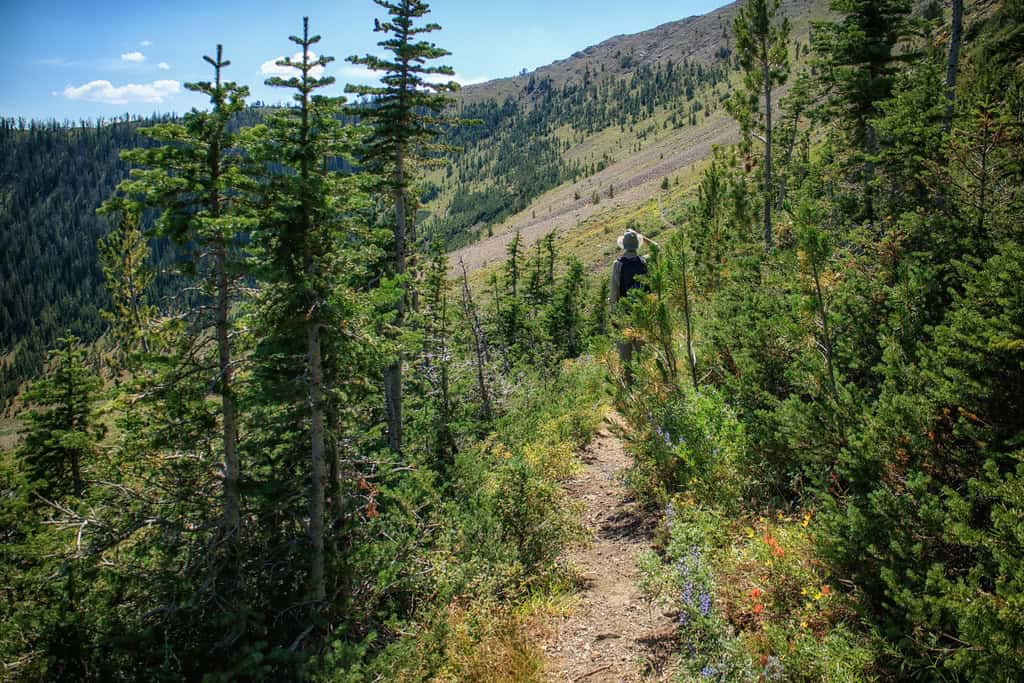
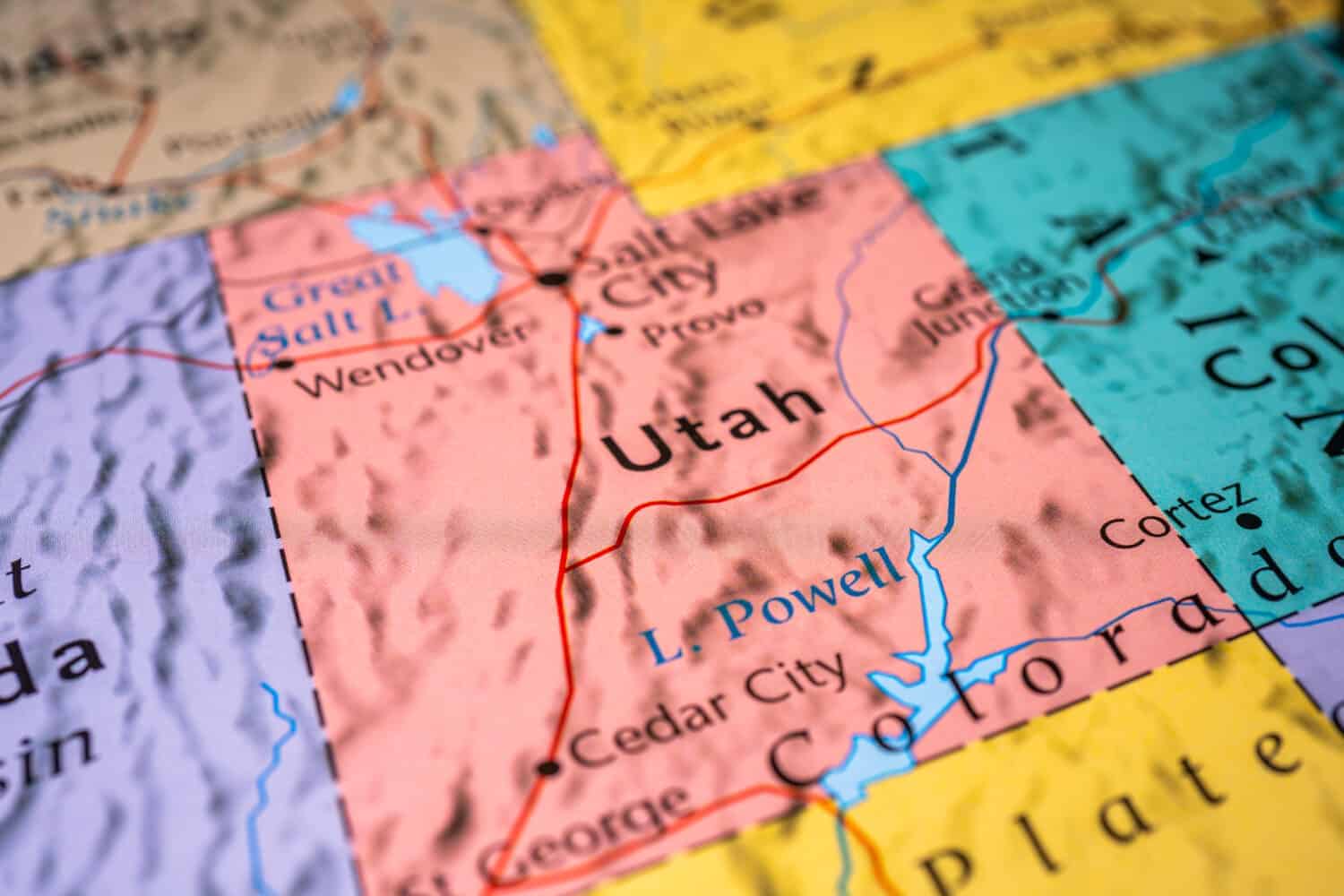
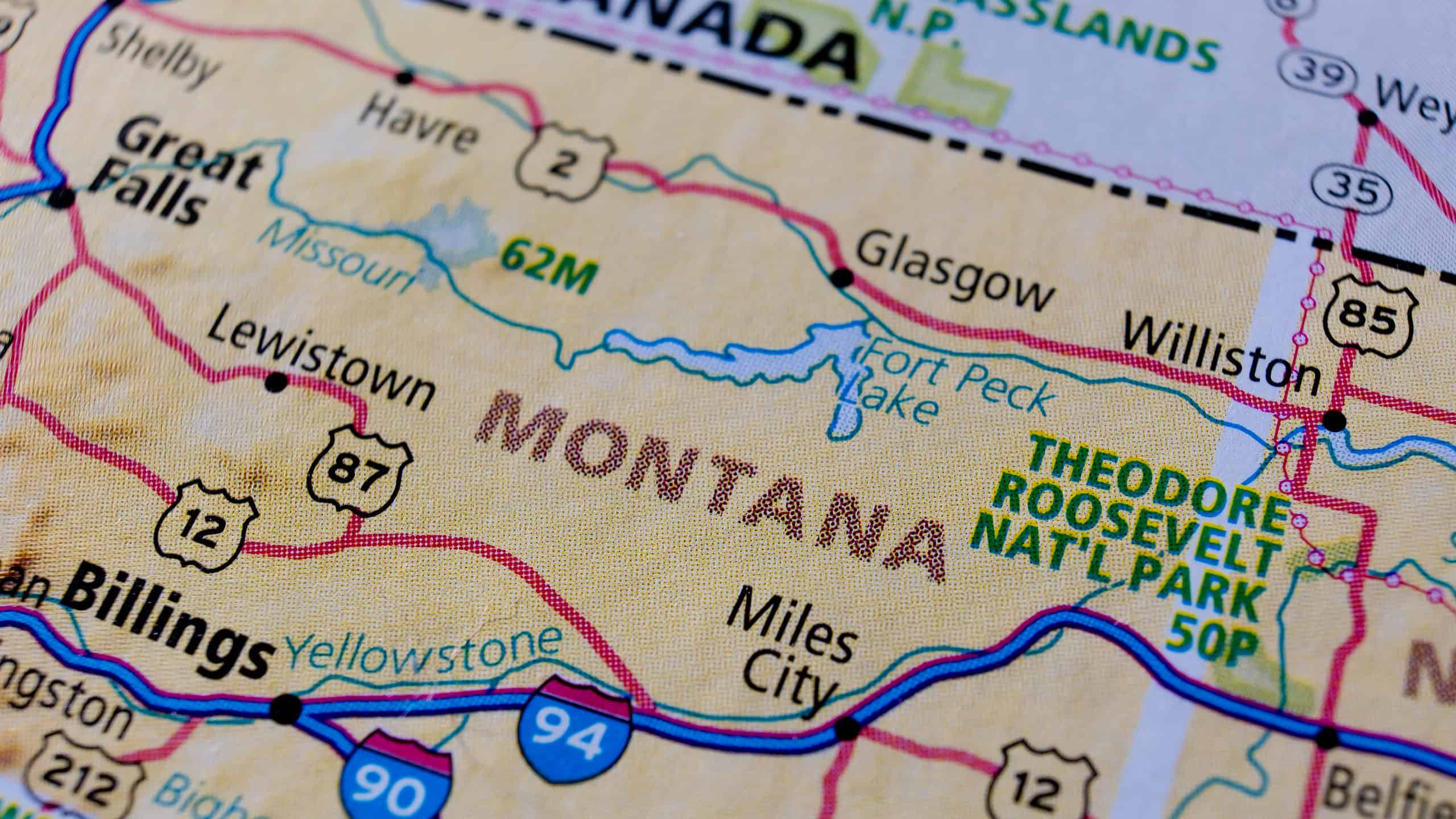
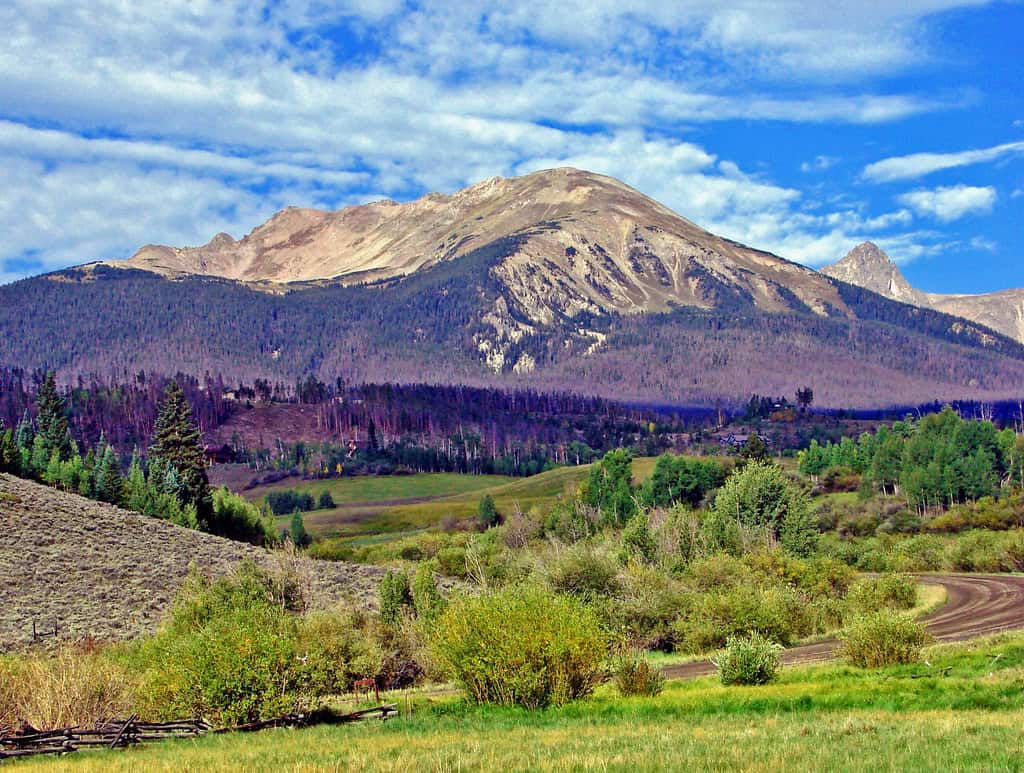
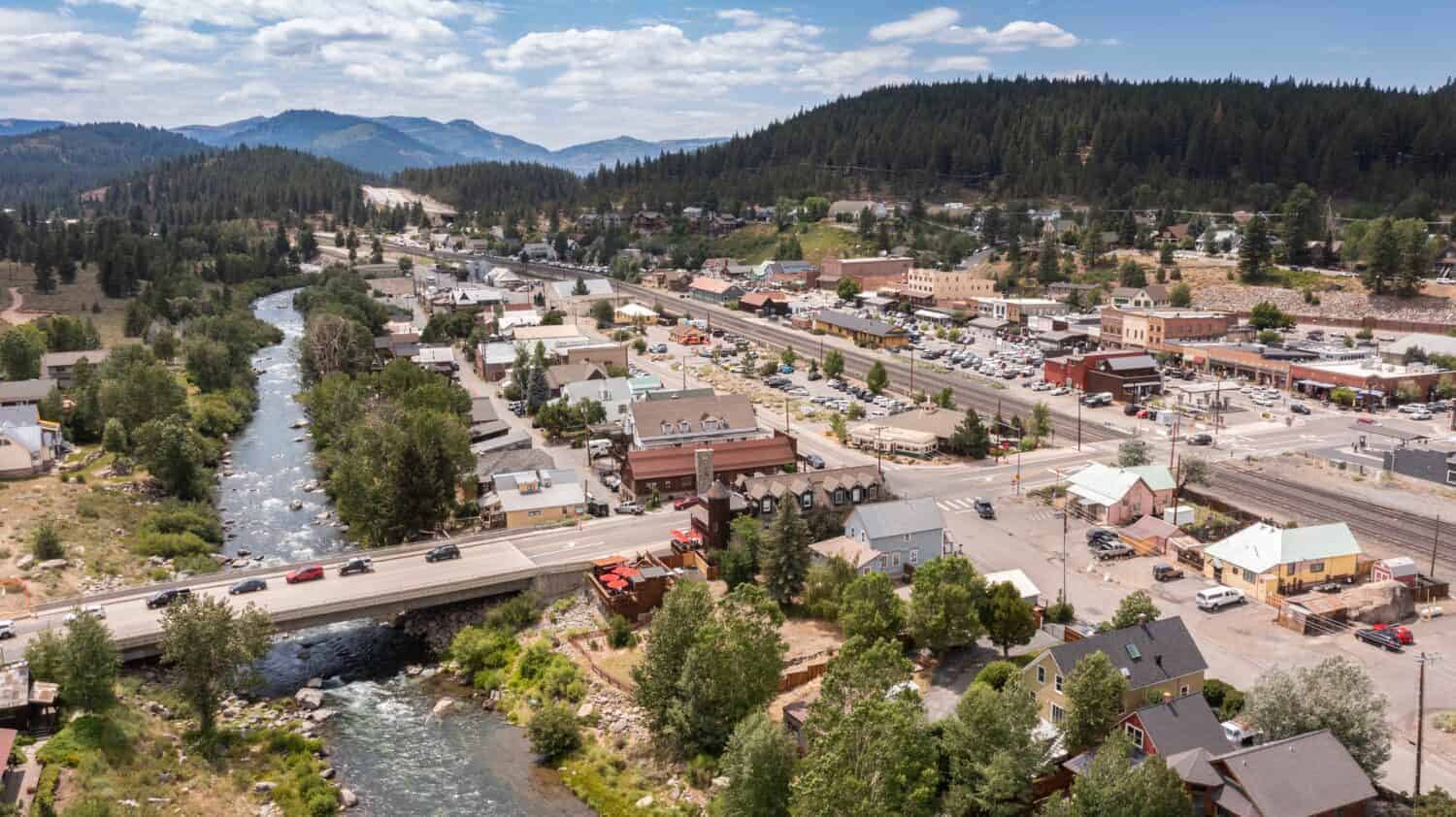
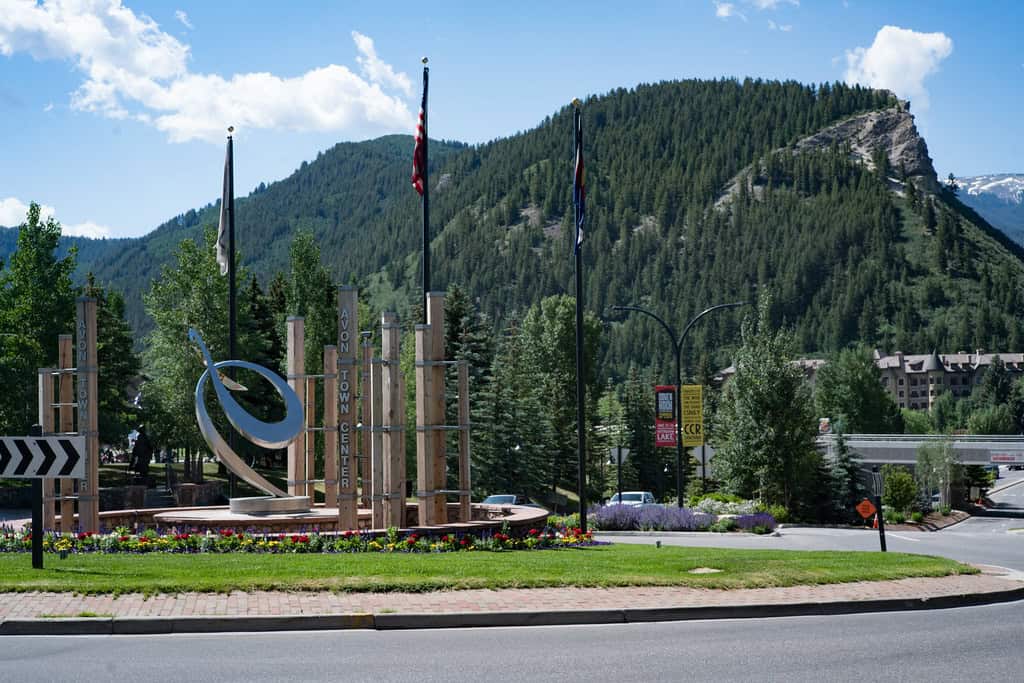
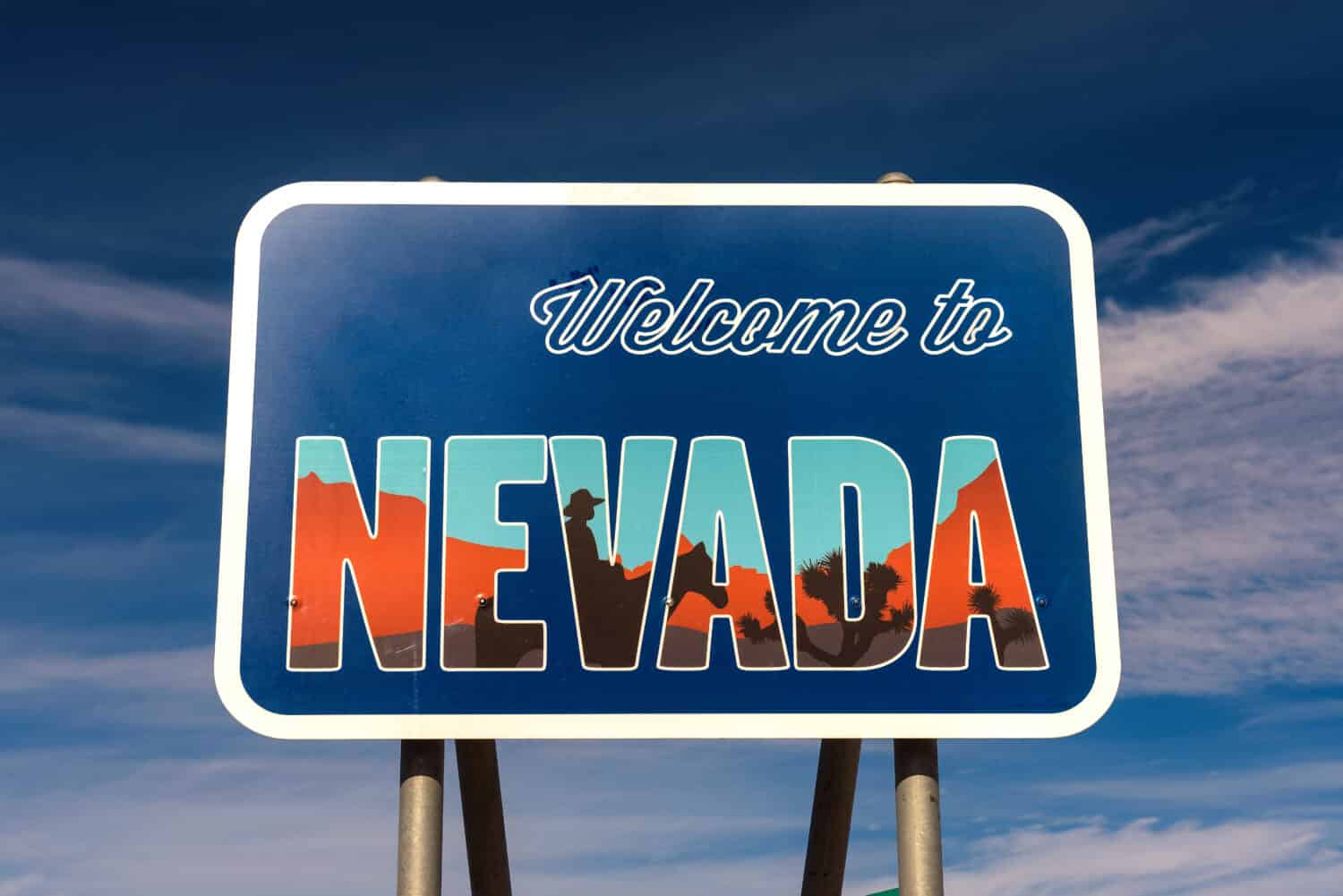
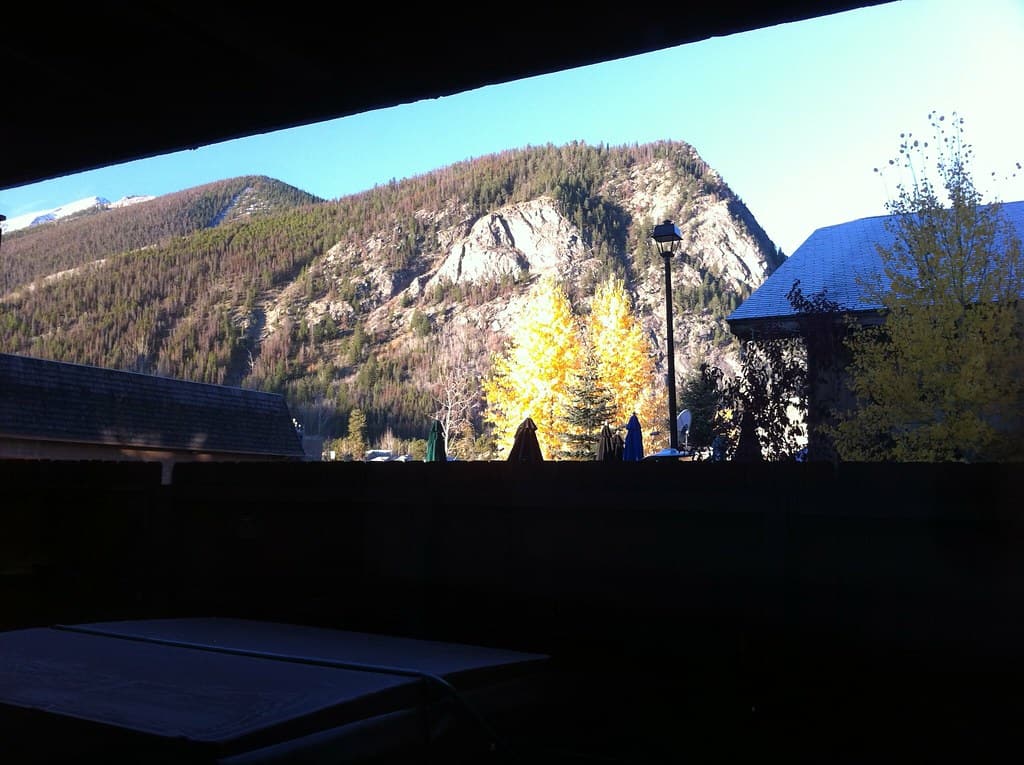
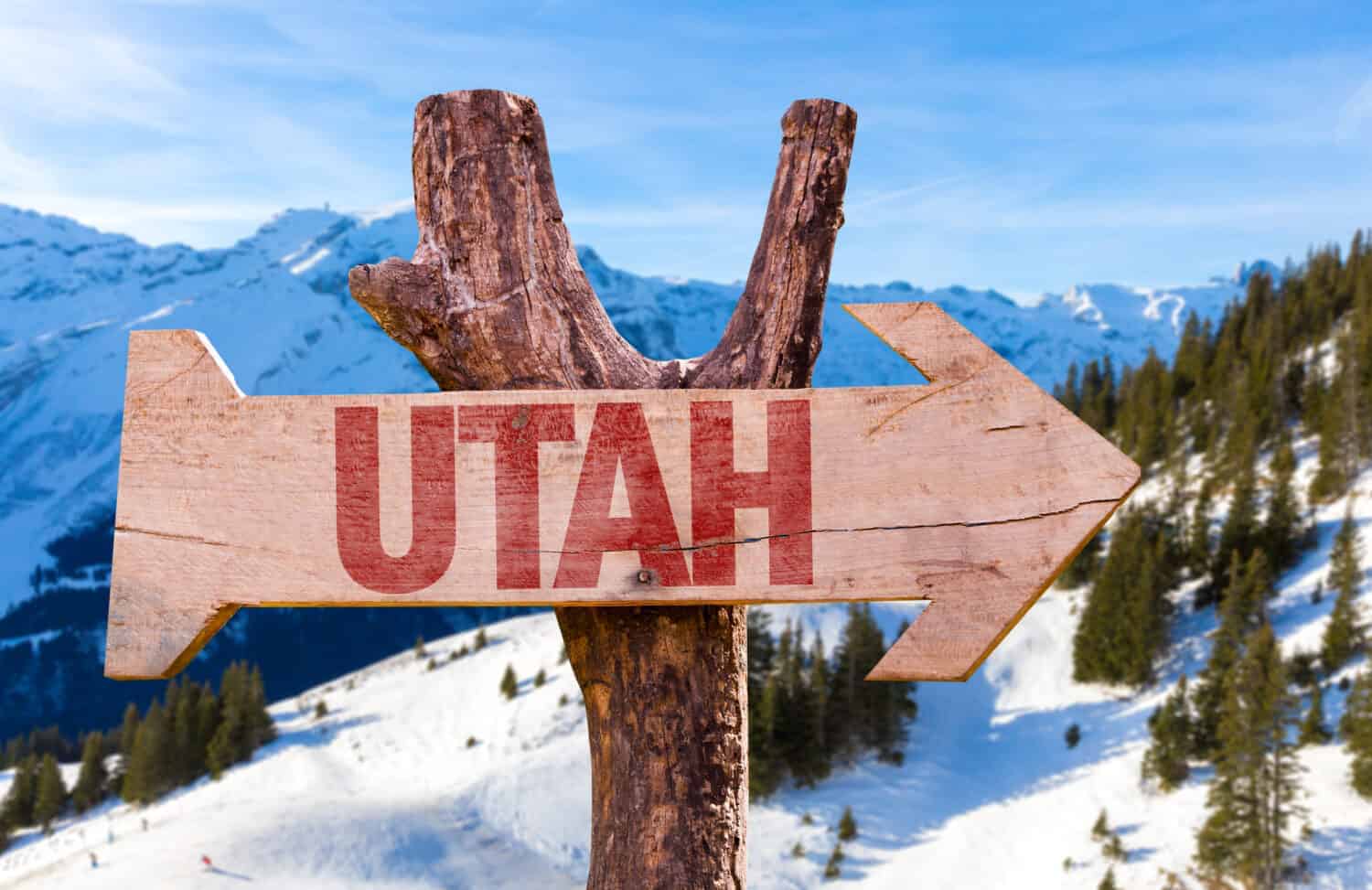
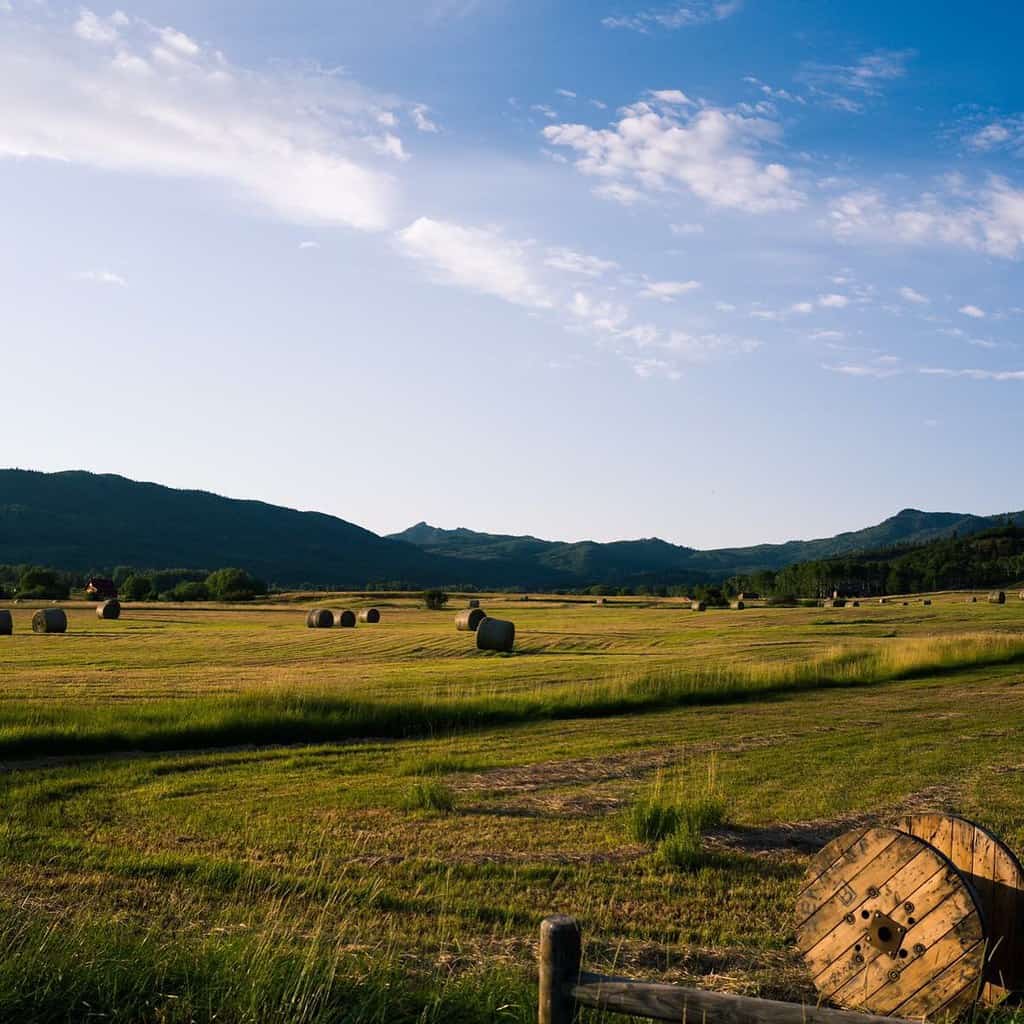
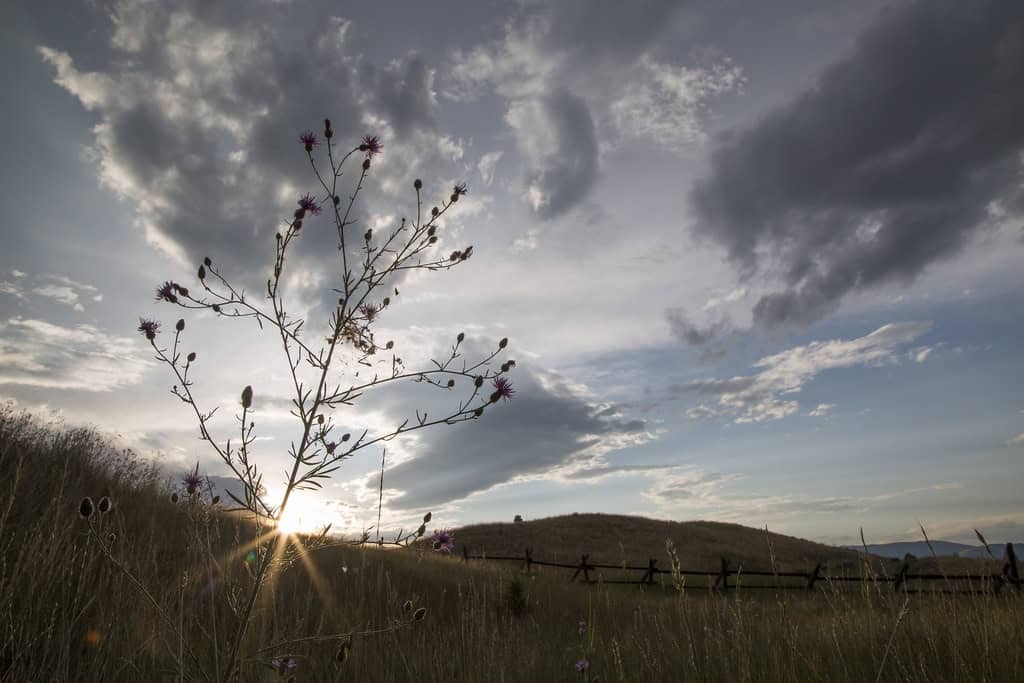

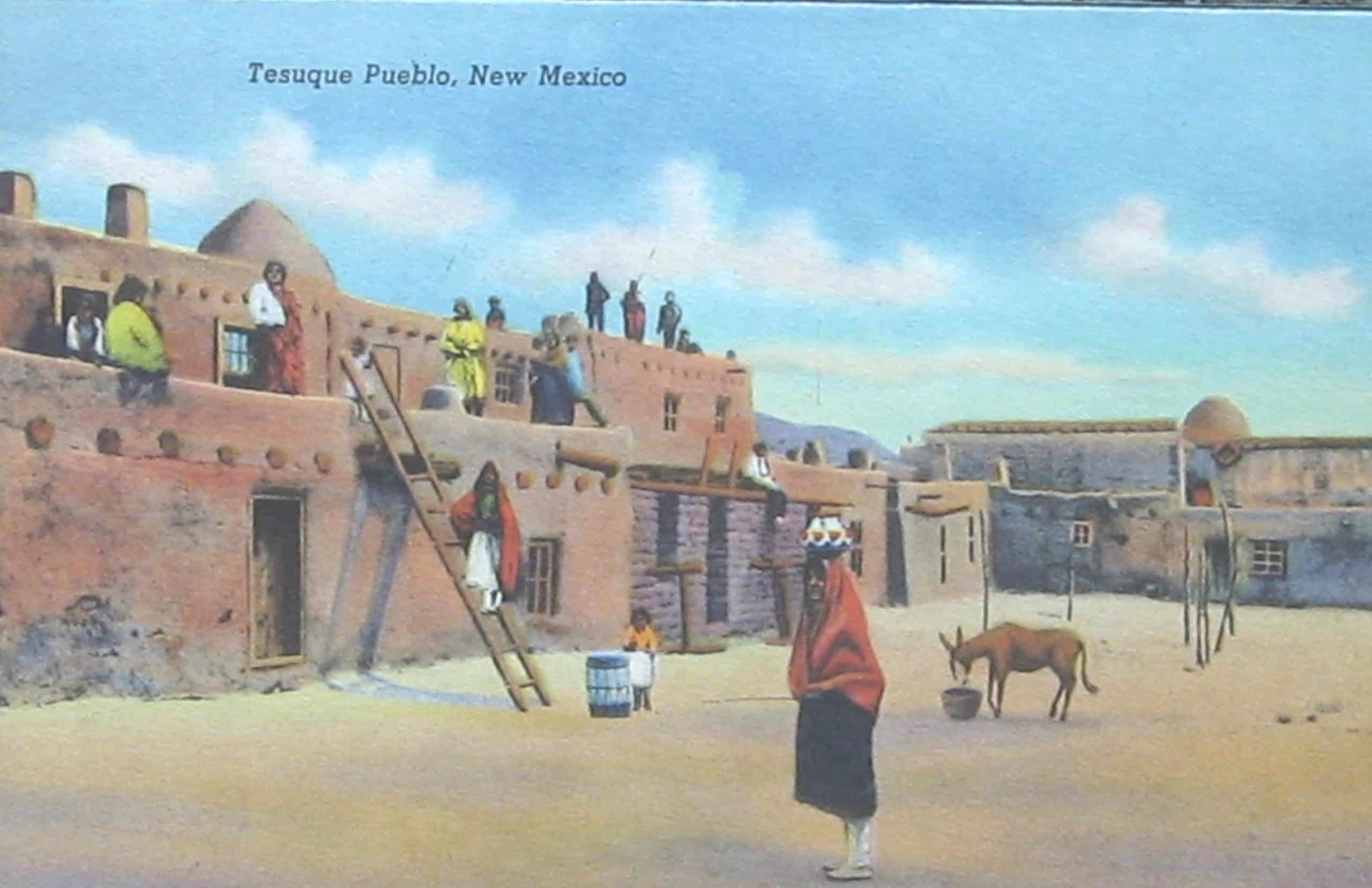
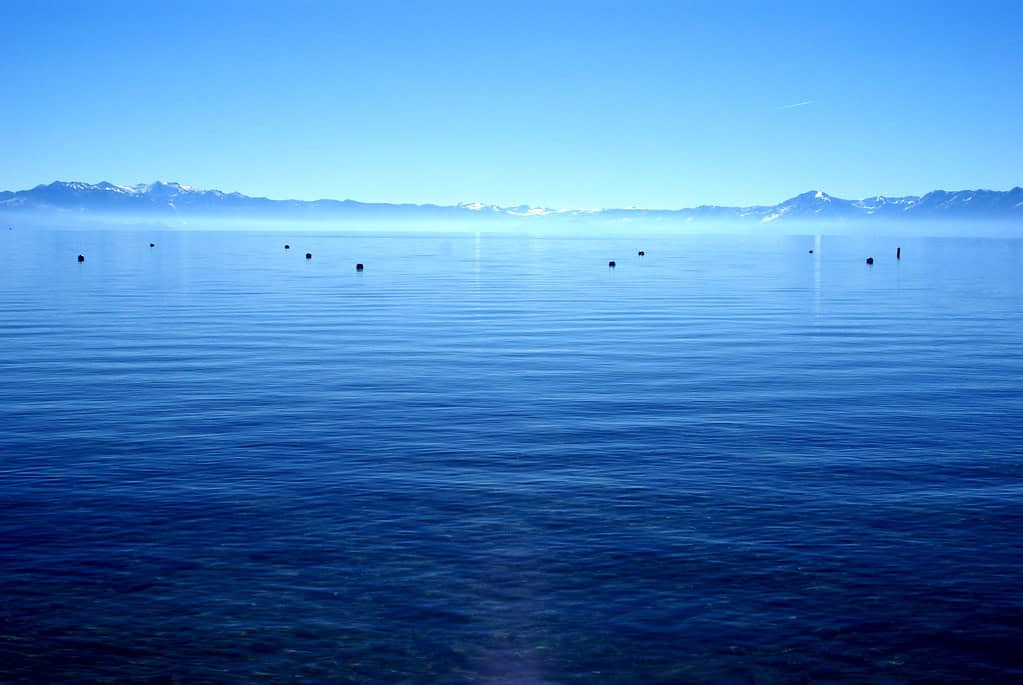
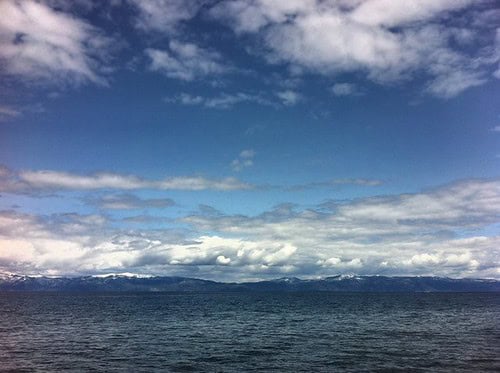


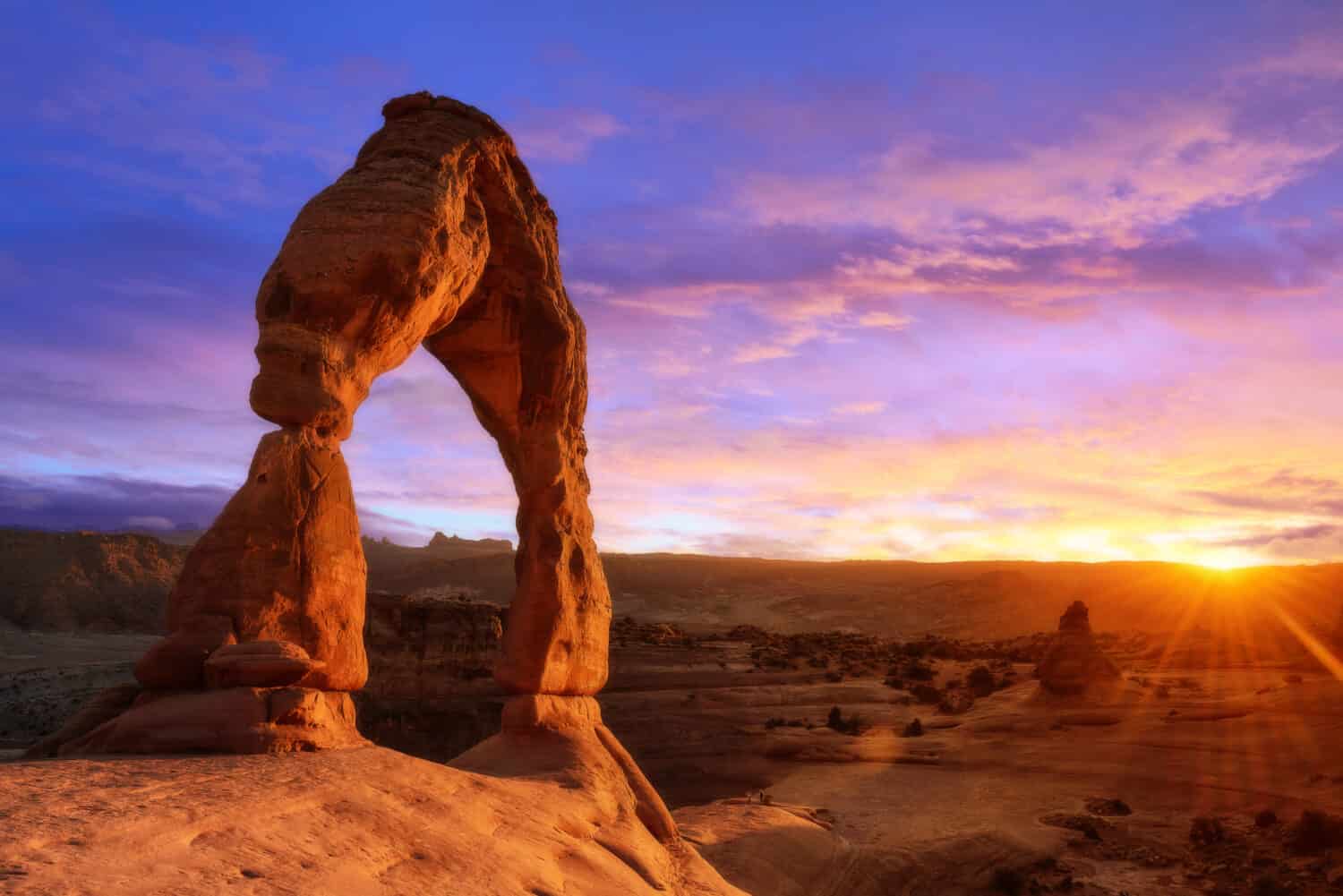
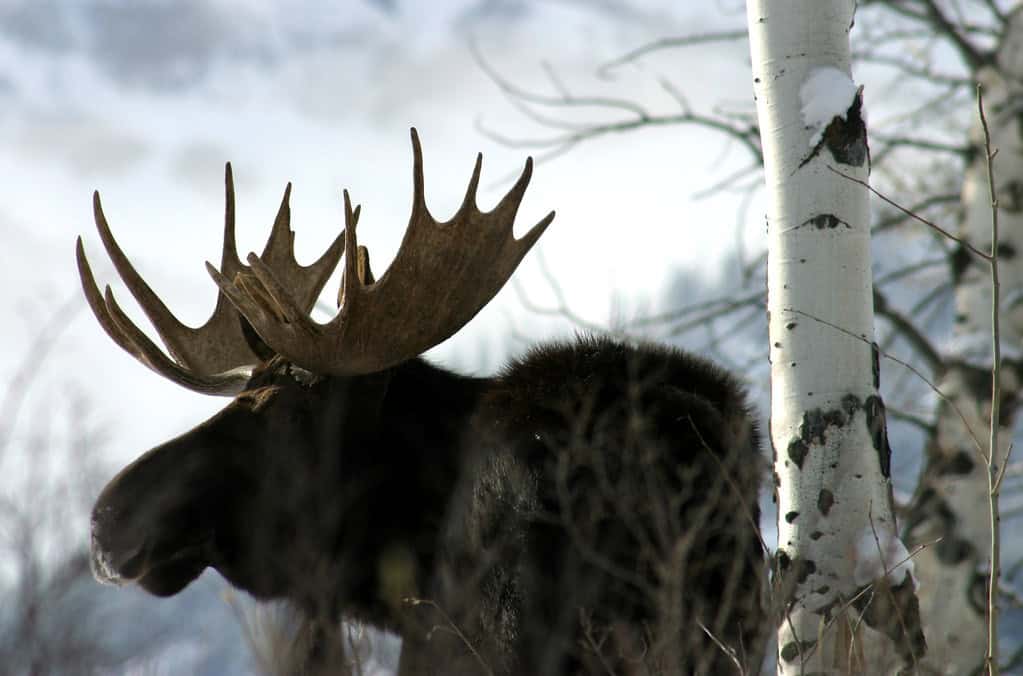
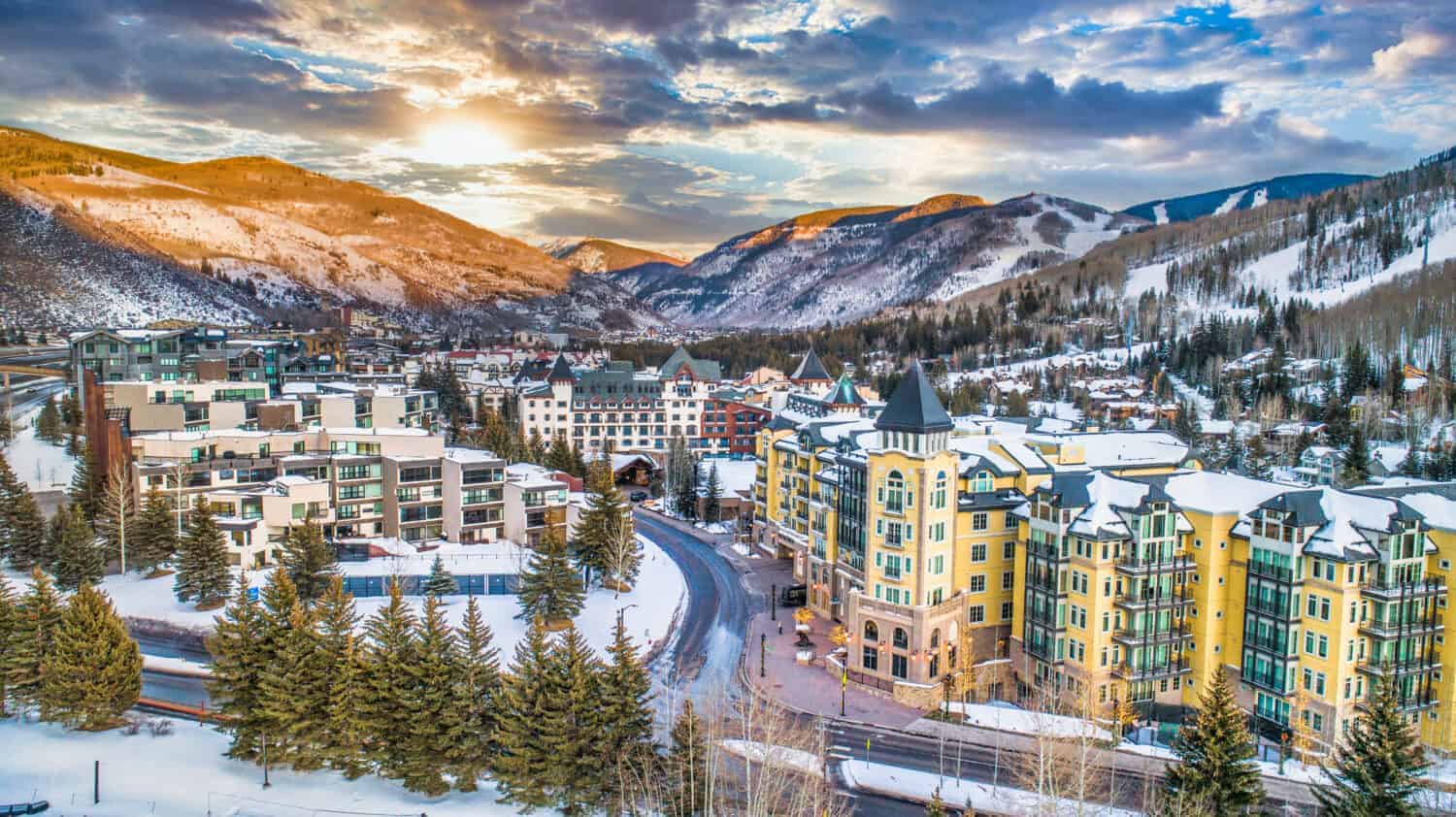
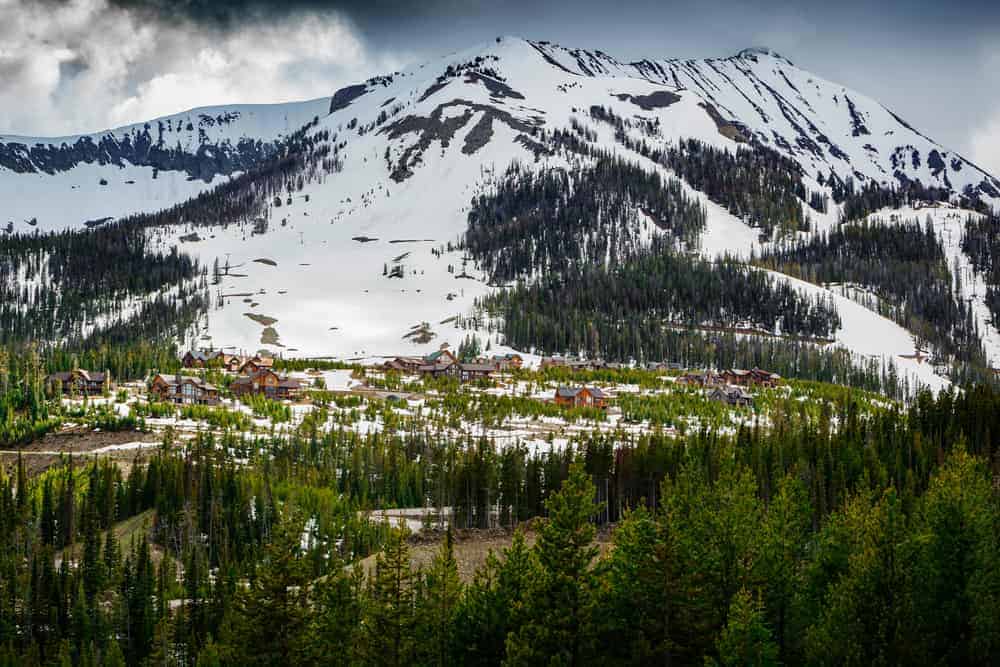
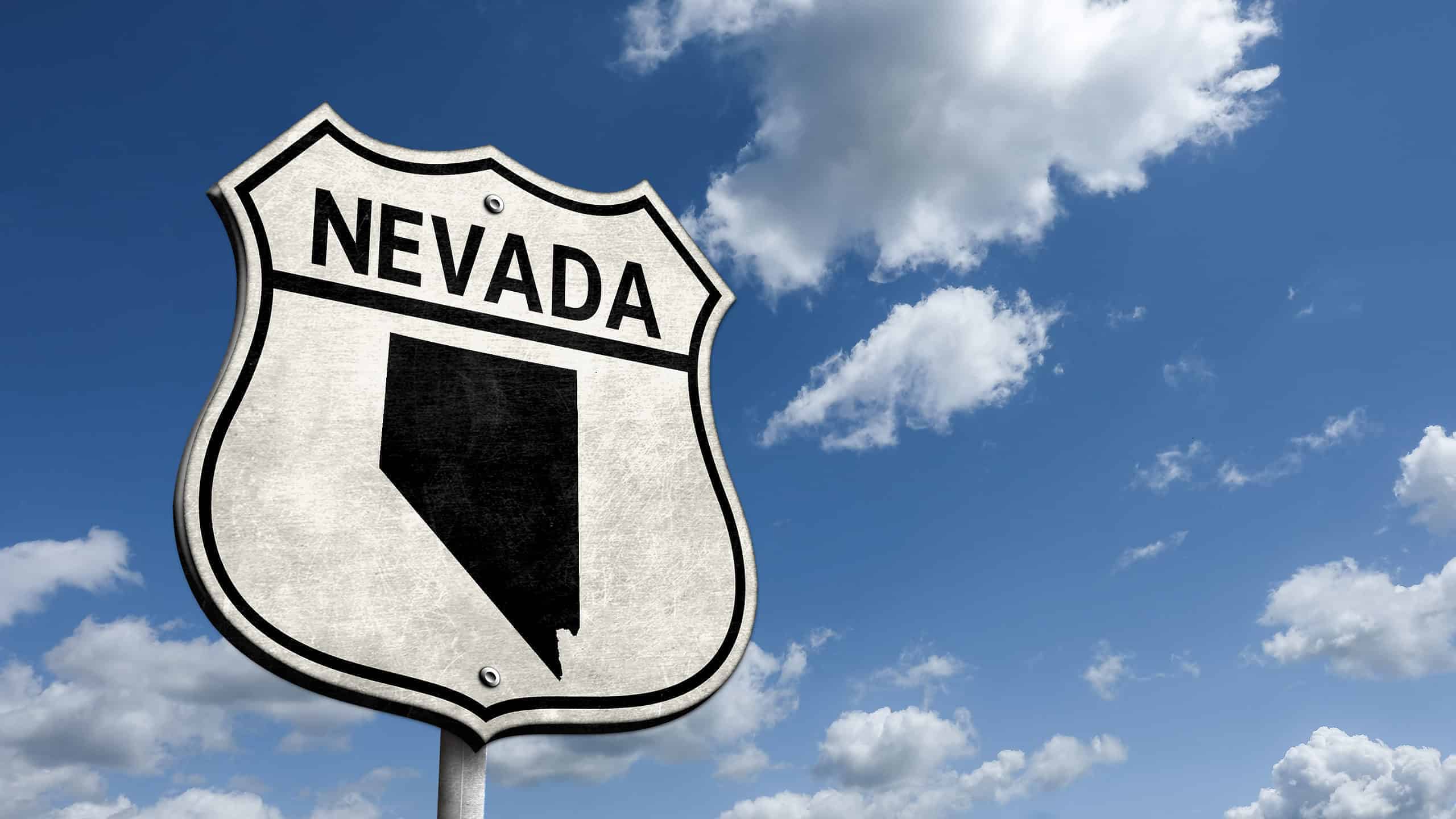
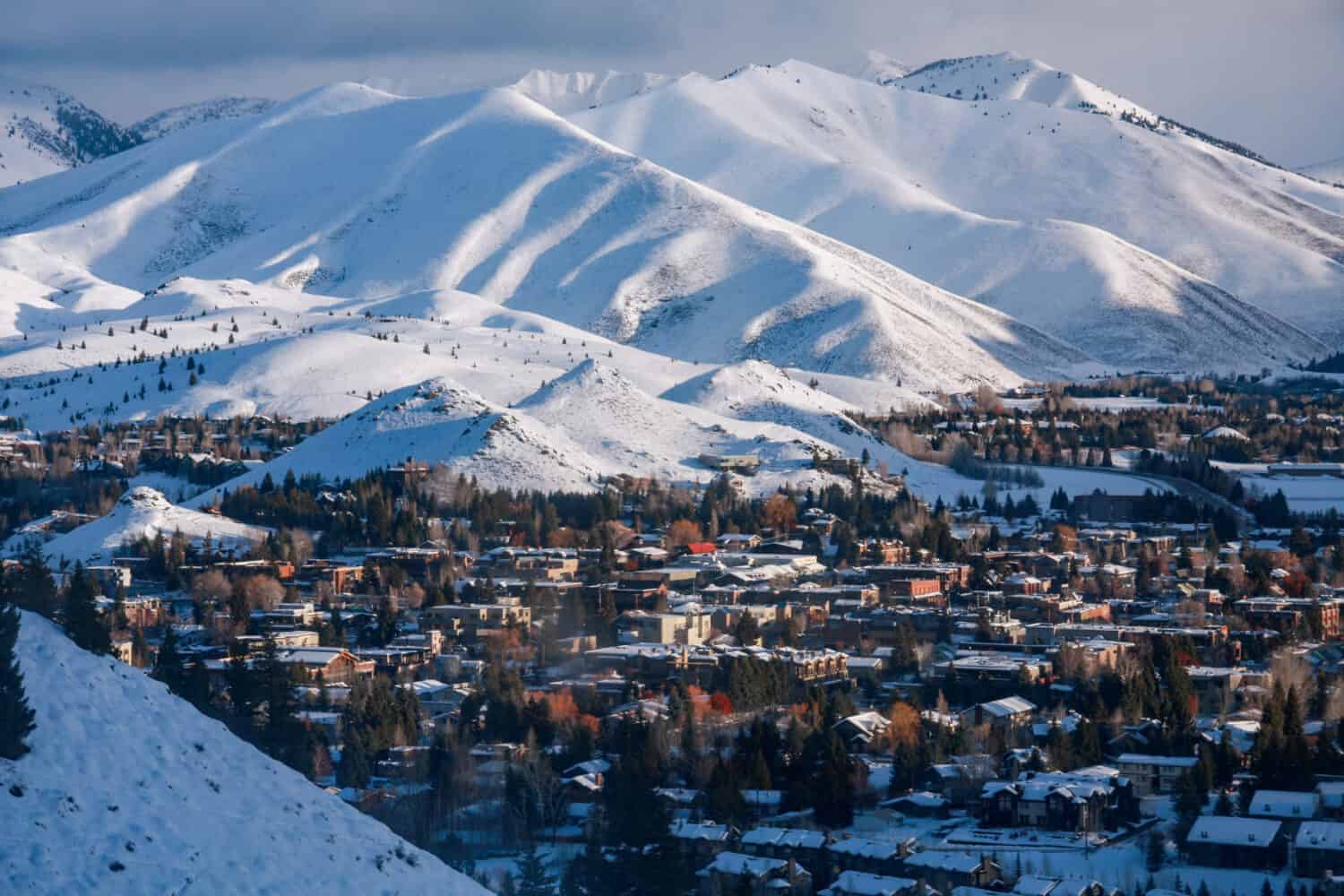
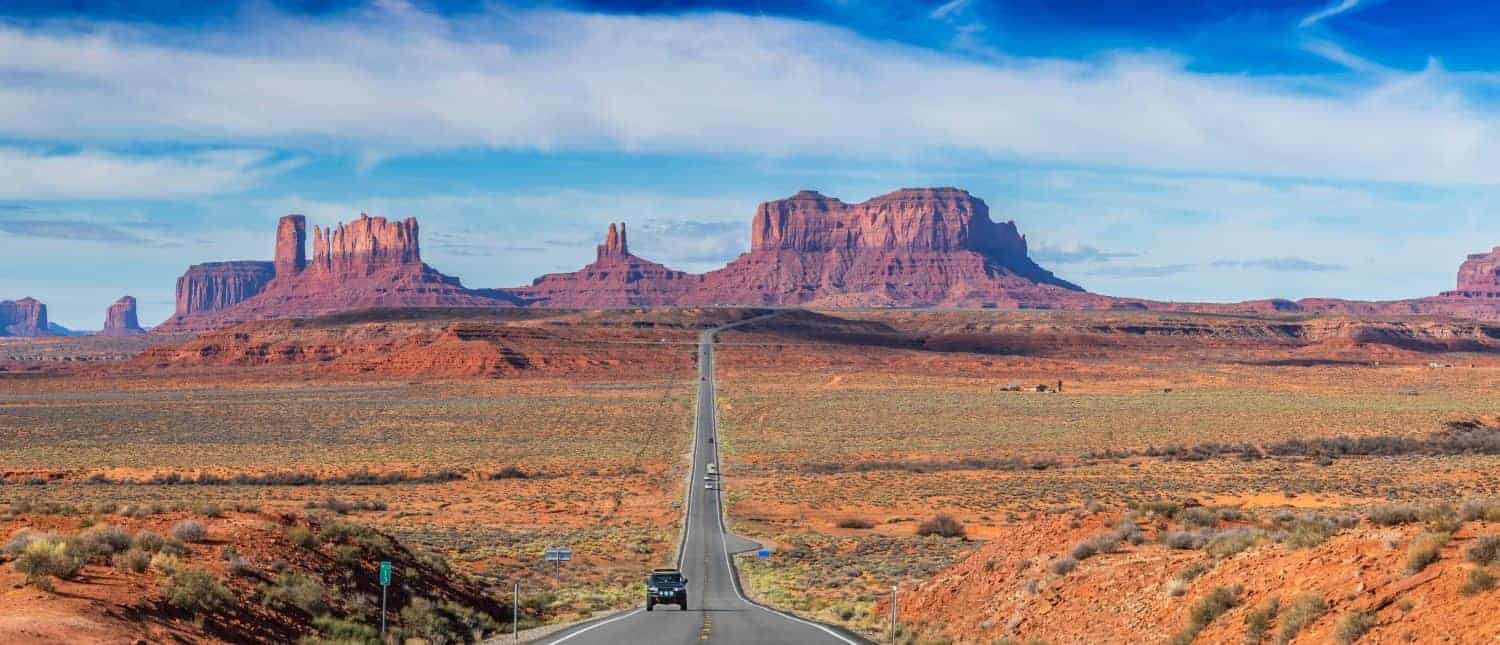

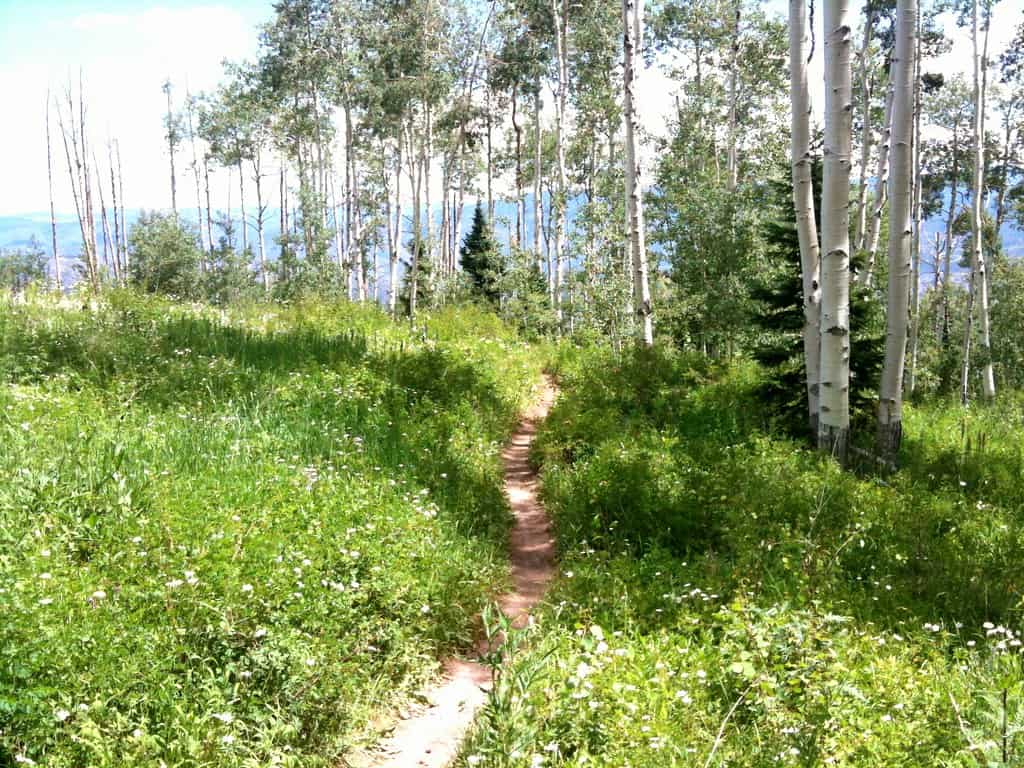

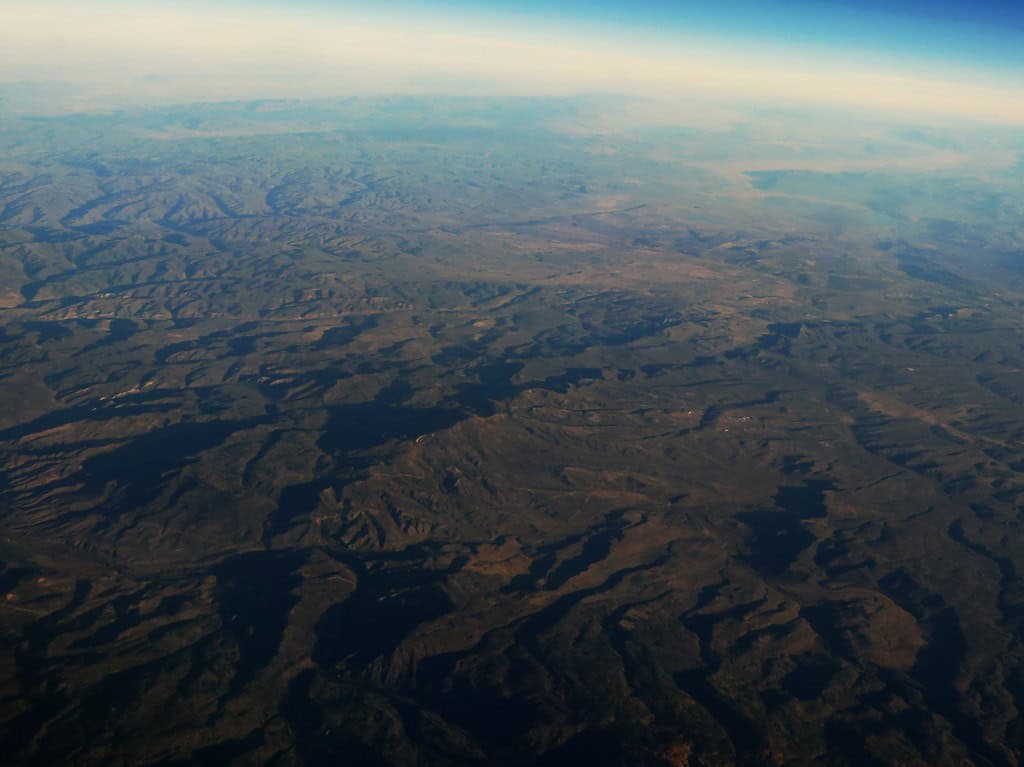
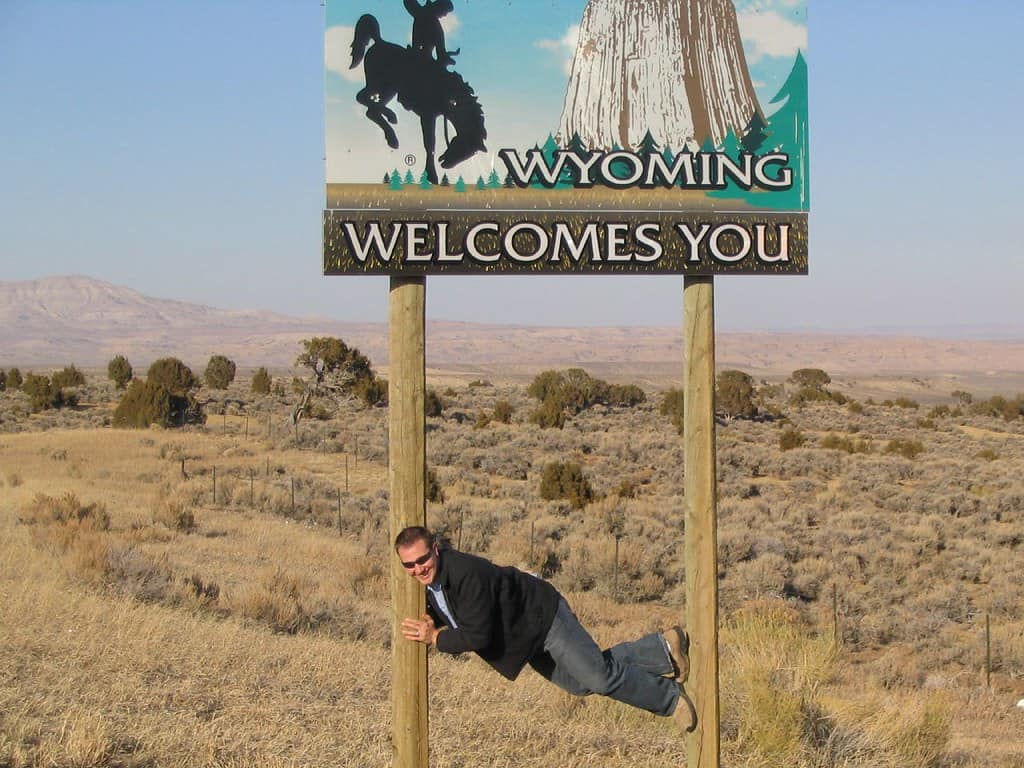
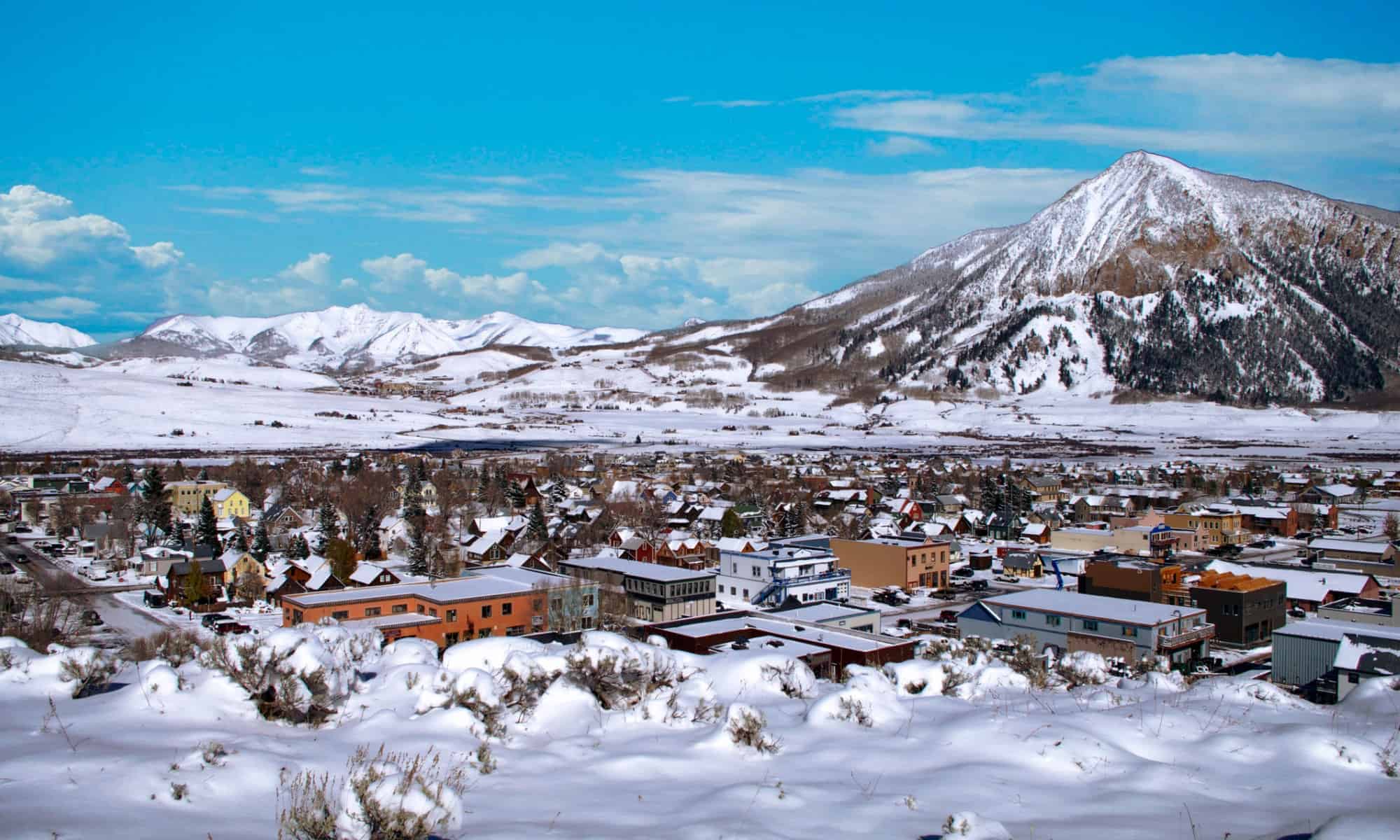
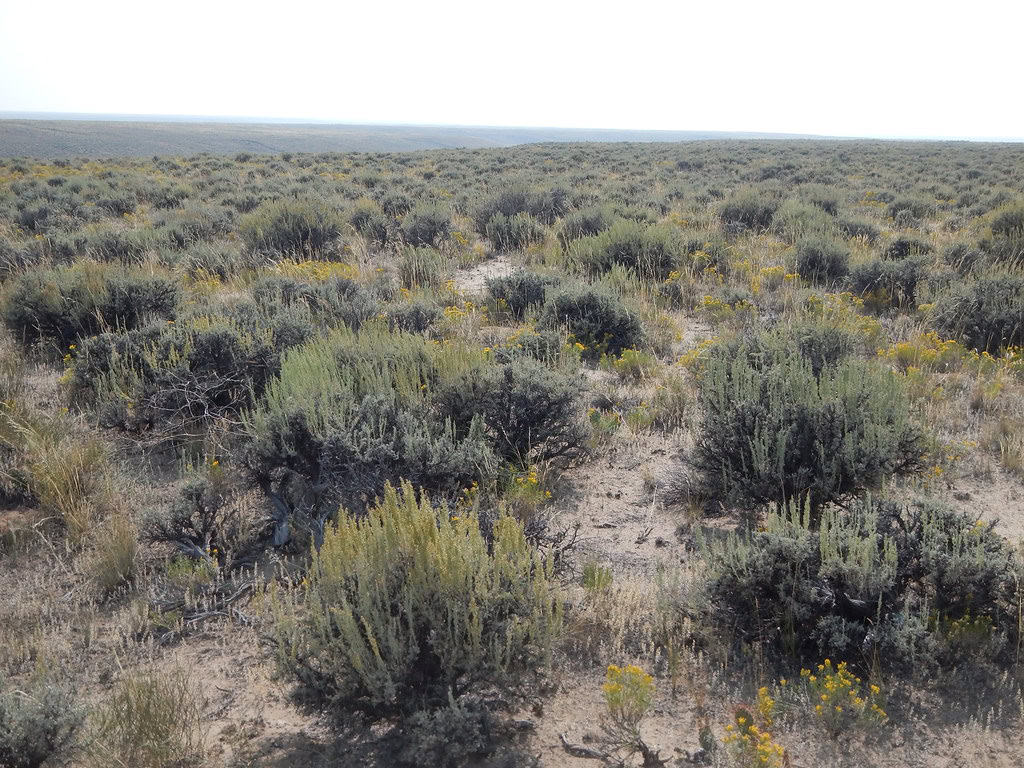
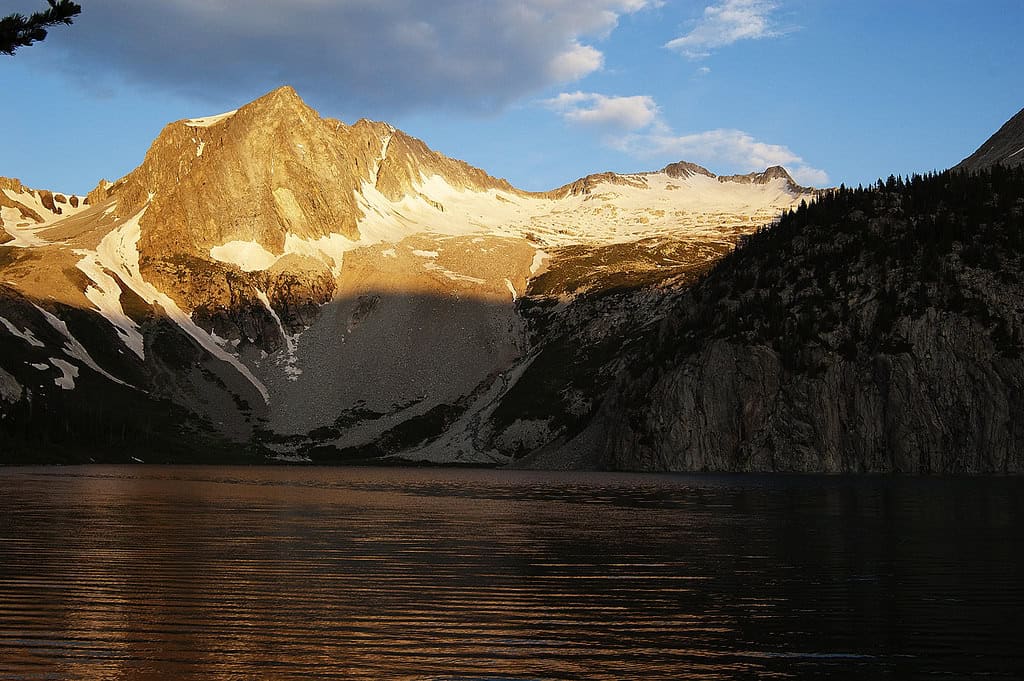
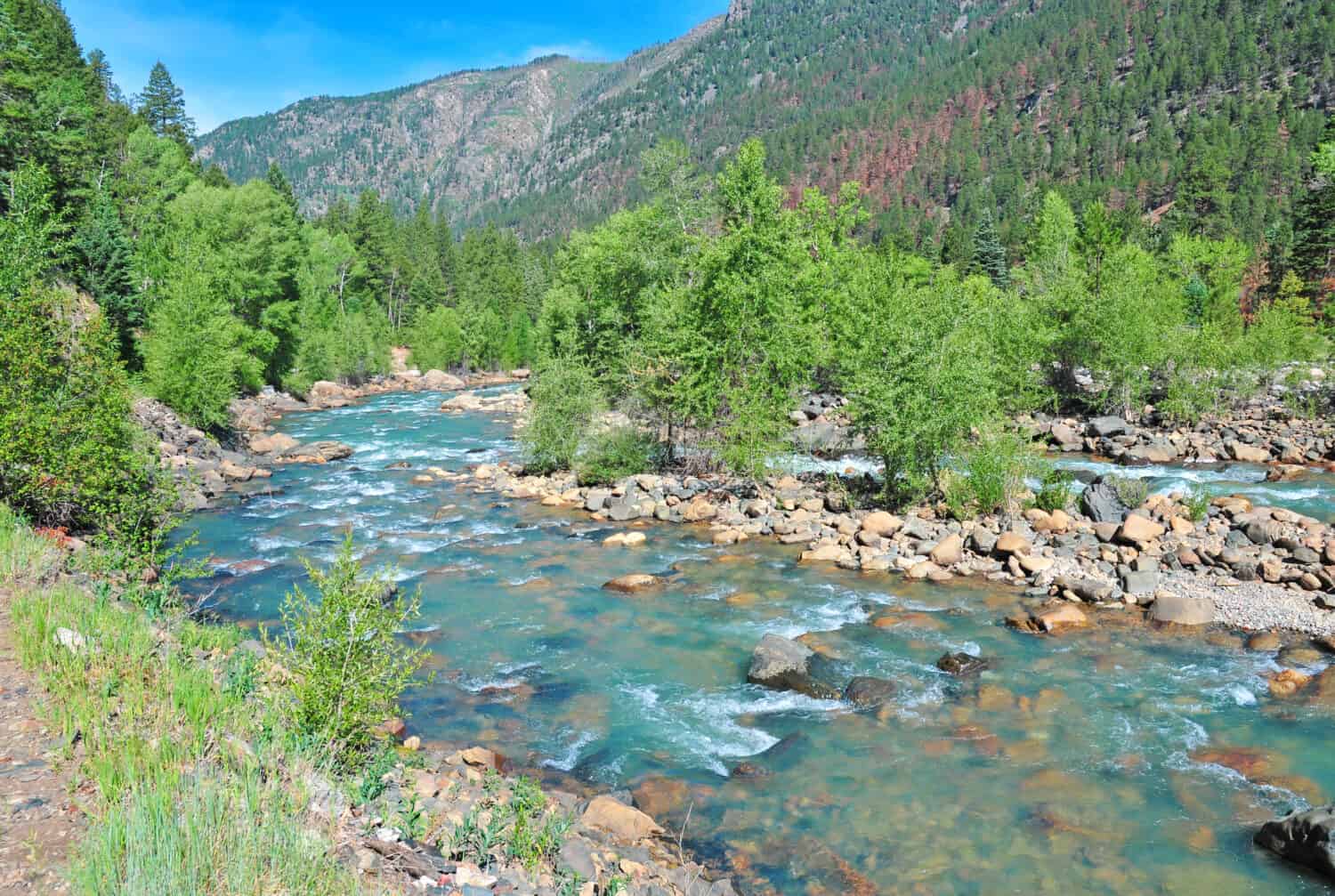
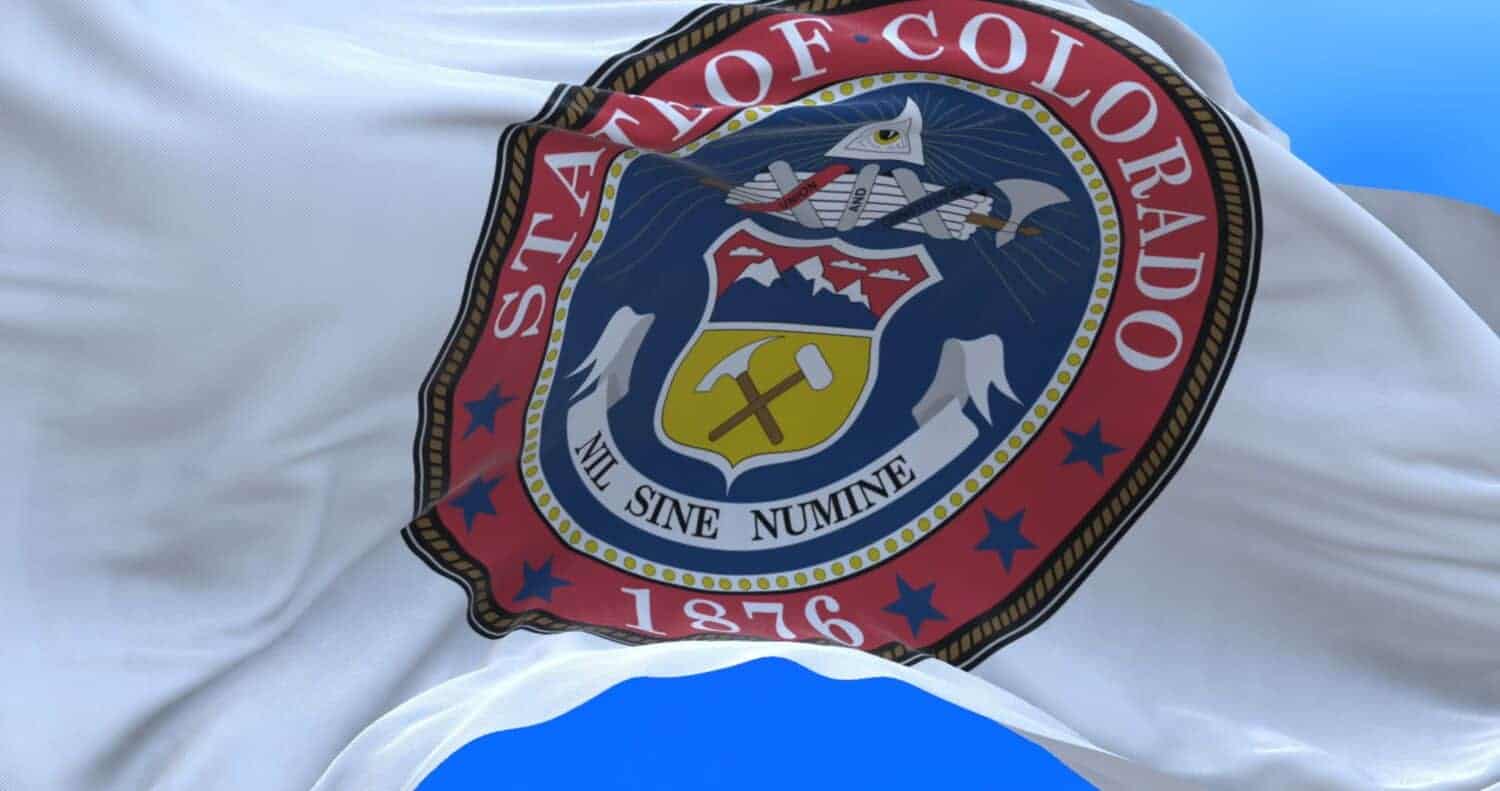
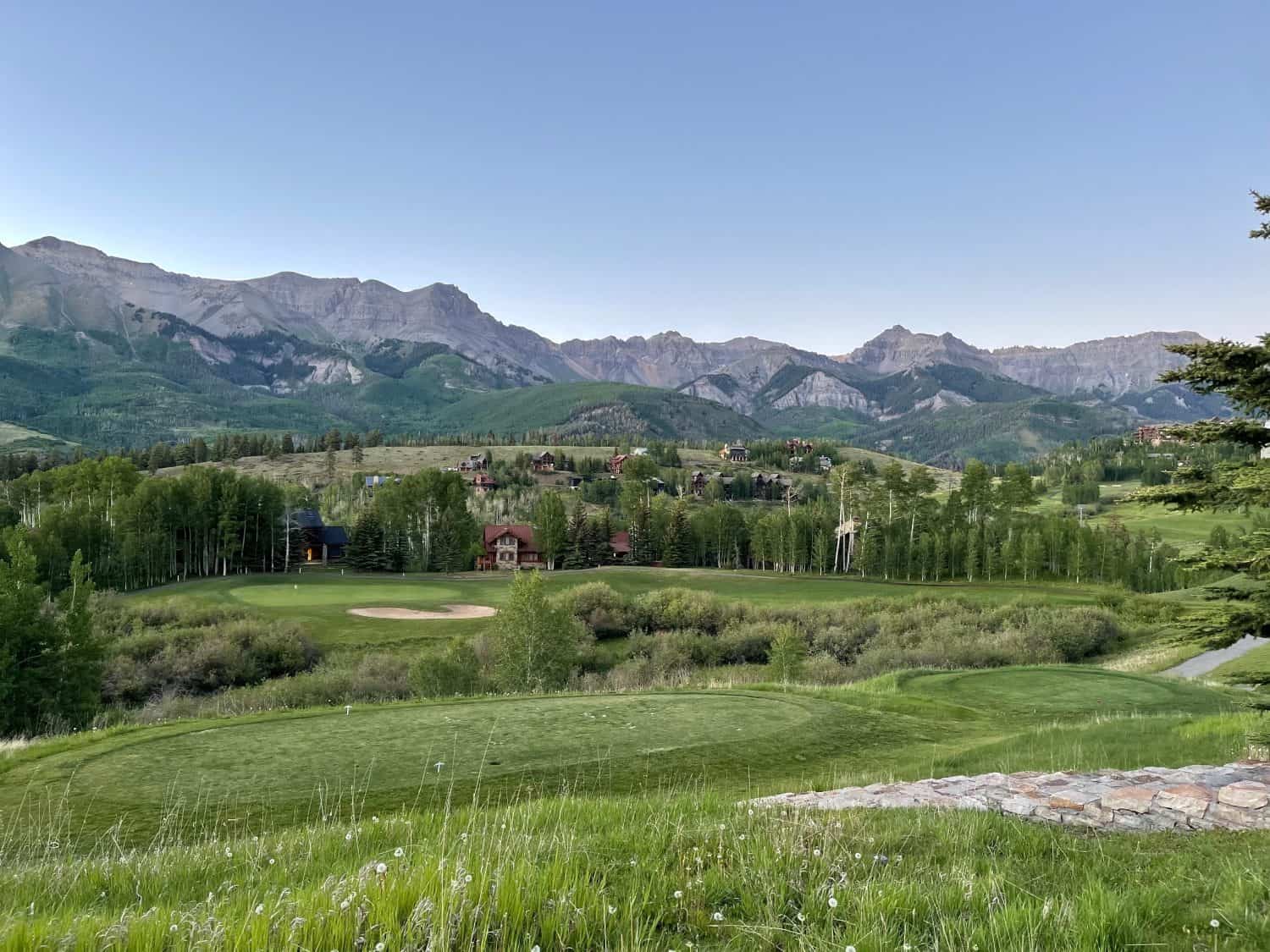
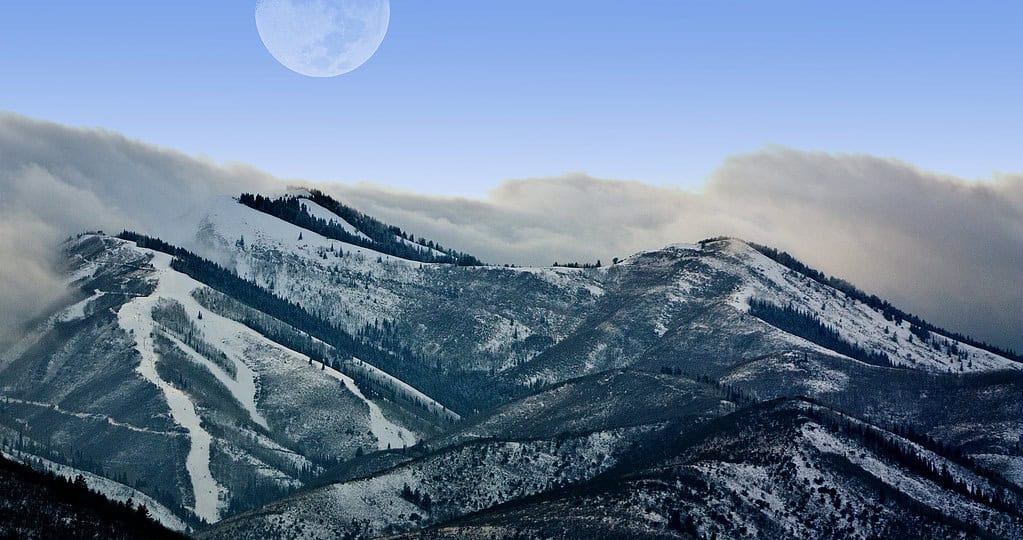
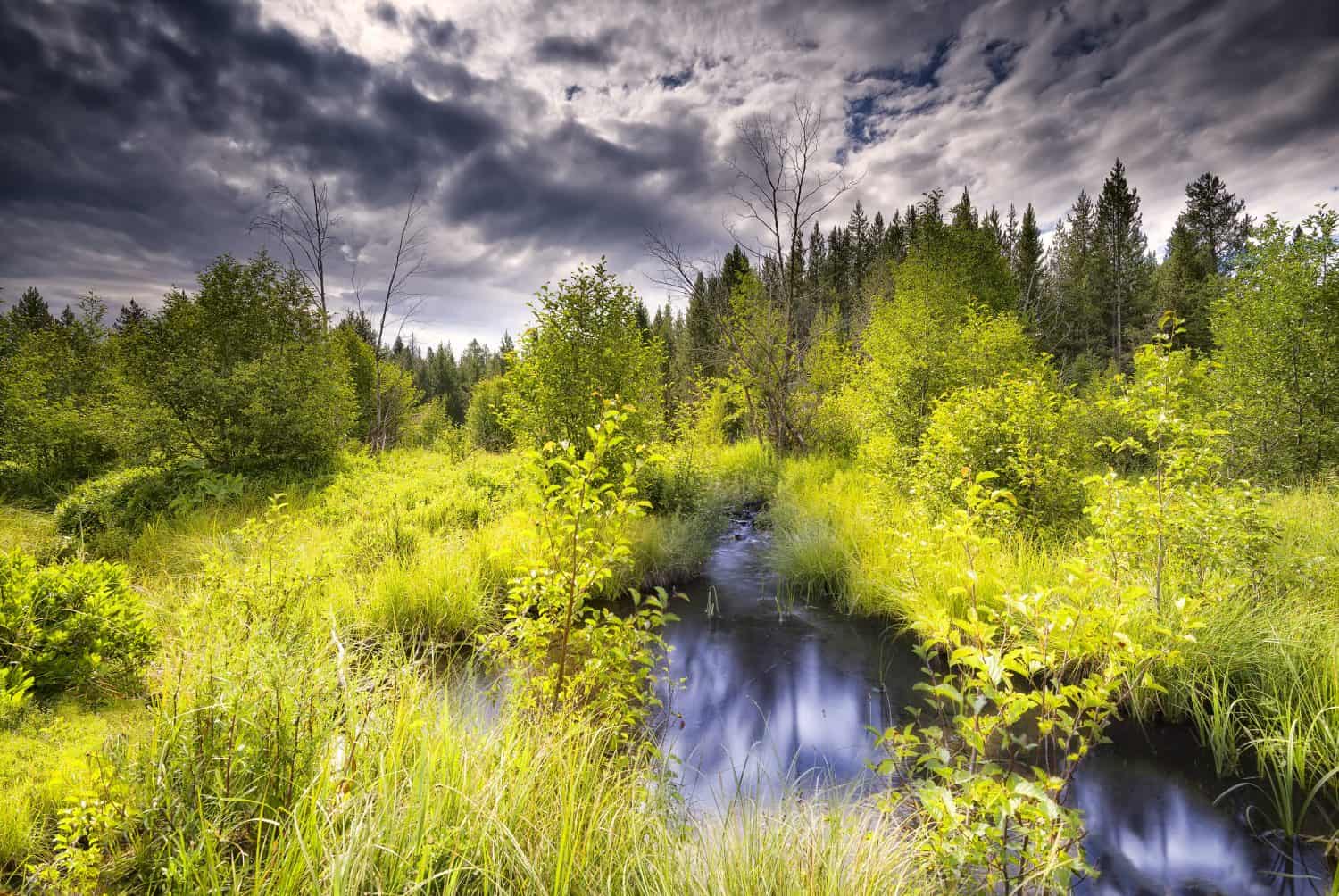
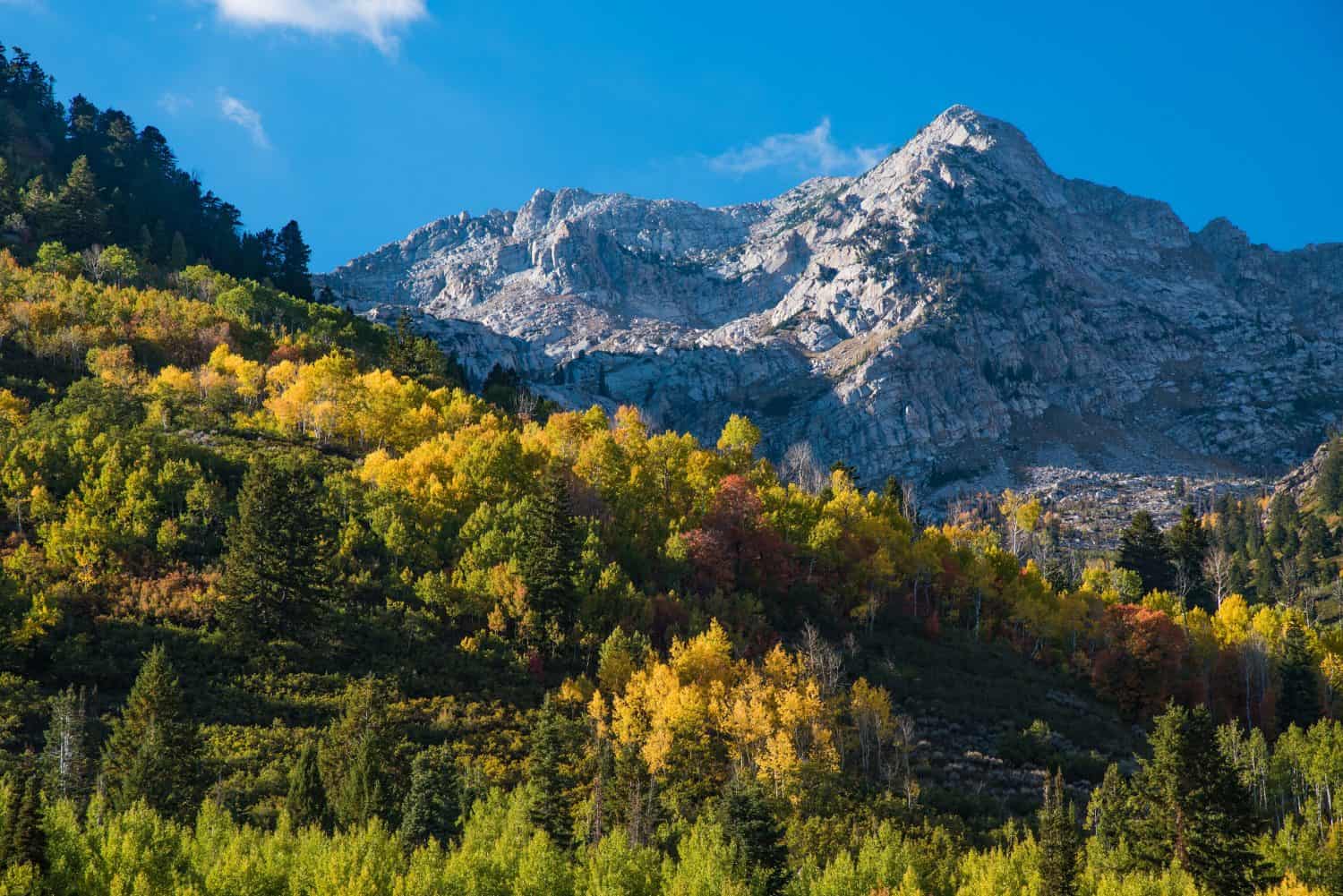
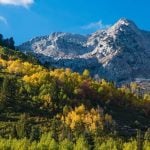
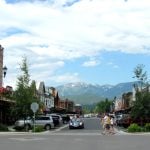
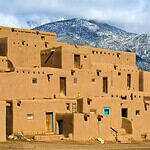
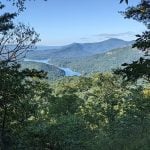
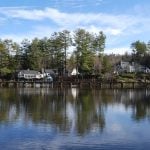
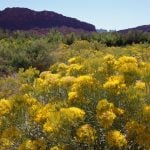
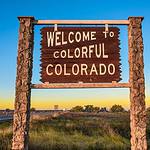
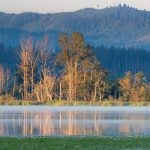
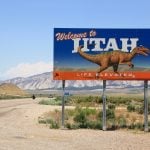
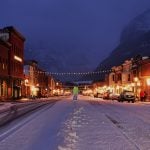
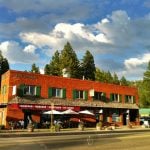
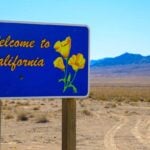
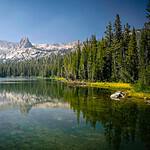
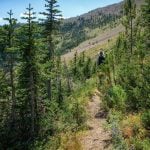
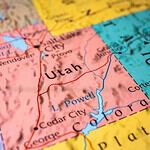
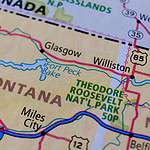
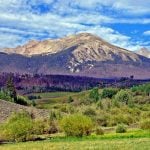
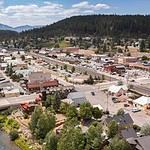

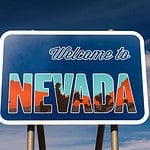
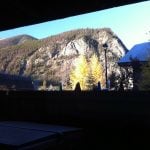
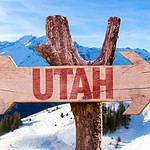
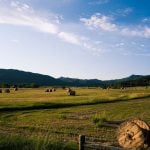
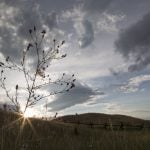
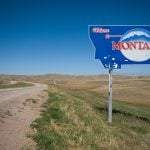
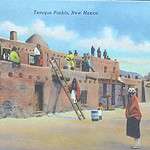
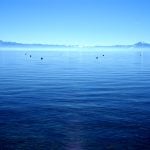
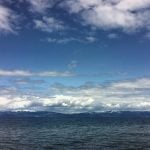
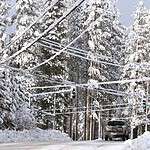
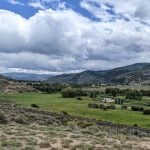

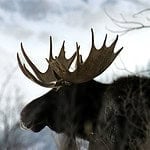
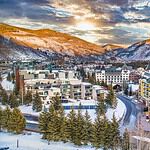
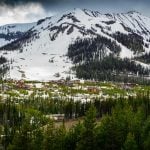
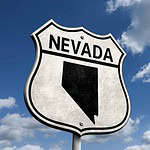
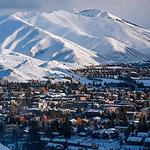
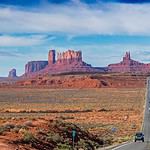
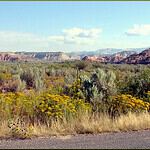
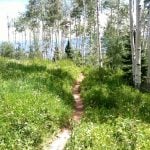
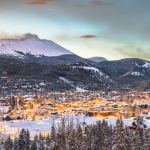
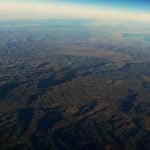
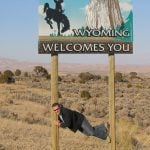
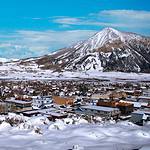
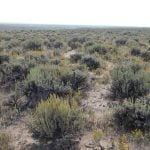
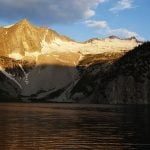
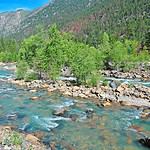

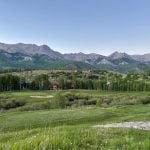
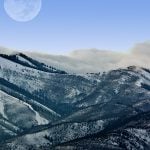
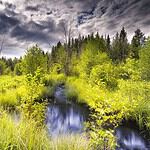
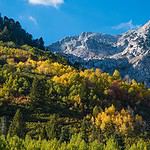
Breathtaking Homes in America's Scenic Mountain Towns
City life isn't for everyone and if you dream of waking up to breathtaking mountain views and being surrounded by nature, a move to a U.S. mountain town might be perfect for you. While some locations may seem out of reach, many offer affordable housing options without sacrificing charm or scenic beauty. These towns have smaller populations, stunning landscapes, and real estate opportunities that make mountain living more accessible than you might think.
Methodology
To determine the U.S. mountain towns with the most beautiful homes, 24/7 Wall St. reviewed five-year data on median household value and median household income from the U.S. Census Bureau’s 2022 American Community Survey. Cities, towns, and Census-designated places were ranked based on the percentage of owner-occupied housing units valued at $2,000,000 or more.
Only places with at least 1,000 residents where at least 5% of housing units are vacant for seasonal or recreational use that intersect a mountain were considered. Mountain spatial boundaries are from the GMBA Mountain Inventory v2 of EarthEnv.
50. Whitefish, MT (Rocky Mountains)
- Homes worth $1,000,000 or more: 15.5%
- Median household income: $69,919
- Total population: 8,098
49. Taos Pueblo, NM (Rocky Mountains)
- Homes worth $1,000,000 or more: 16.5%
- Median household income: $36,597
- Total population: 1,422
48. Lake Lure, NC (Blue Ridge)
- Homes worth $1,000,000 or more: 17.7%
- Median household income: $75,259
- Total population: 1,575
47. Highlands, NC (Blue Ridge)
- Homes worth $1,000,000 or more: 18.0%
- Median household income: $55,573
- Total population: 1,140
46. Wolf Creek, UT (Wasatch Range)
Homes worth $1,000,000 or more: 18.4%
Median household income: $137,813
Total population: 1,642
45. Kittredge, CO (Front Range)
- Homes worth $1,000,000 or more: 18.8%
- Median household income: $143,147
- Total population: 1,021
44. Clear Lake, WA (Cascade Range)
- Homes worth $1,000,000 or more: 19.6%
- Median household income: $94,755
- Total population: 1,157
43. Oakley, UT (Rocky Mountains)
- Homes worth $1,000,000 or more: 19.7%
- Median household income: $119,231
- Total population: 1,744
42. Telluride, CO (Rocky Mountains)
- Homes worth $1,000,000 or more: 21.2%
- Median household income: $81,429
- Total population: 2,622
41. Kings Beach, CA (Sierra Nevada)
- Homes worth $1,000,000 or more: 22.3%
- Median household income: $50,220
- Total population: 2,589
40. Tahoma, CA (Sierra Nevada)
- Homes worth $1,000,000 or more: 23.1%
- Median household income: $83,971
- Total population: 1,071
39. Mammoth Lakes, CA (Sierra Nevada)
- Homes worth $1,000,000 or more: 23.6%
- Median household income: $80,795
- Total population: 7,253
38. Ketchum, ID (Rocky Mountains)
- Homes worth $1,000,000 or more: 23.9%
- Median household income: $87,478
- Total population: 3,490
37. Midway, UT (Wasatch Range)
- Homes worth $1,000,000 or more: 25.6%
- Median household income: $130,648
- Total population: 6,019
36. Somers, MT (Rocky Mountains)
- Homes worth $1,000,000 or more: 27.1%
- Median household income: $54,466
- Total population: 1,037
35. Silverthorne, CO (Rocky Mountains)
- Homes worth $1,000,000 or more: 28.7%
- Median household income: $97,558
- Total population: 4,550
34. Truckee, CA (Sierra Nevada)
- Homes worth $1,000,000 or more: 28.9%
- Median household income: $107,423
- Total population: 16,784
33. Avon, CO (Rocky Mountains)
- Homes worth $1,000,000 or more: 29.1%
- Median household income: $85,817
- Total population: 6,115
32. Kingsbury, NV (Sierra Nevada)
- Homes worth $1,000,000 or more: 29.4%
- Median household income: $74,424
- Total population: 1,920
31. Frisco, CO (Rocky Mountains)
- Homes worth $1,000,000 or more: 31.1%
- Median household income: $101,140
- Total population: 2,900
30. Hideout, UT (Wasatch Range)
- Homes worth $1,000,000 or more: 32.3%
- Median household income: $73,472
- Total population: 1,066
29. Steamboat Springs, CO (Rocky Mountains)
- Homes worth $1,000,000 or more: 33.5%
- Median household income: $93,280
- Total population: 13,251
28. Pray, MT (Rocky Mountains)
- Homes worth $1,000,000 or more: 34.2%
- Median household income: $104,512
- Total population: 1,017
27. Lakeside, MT (Rocky Mountains)
- Homes worth $1,000,000 or more: 35.6%
- Median household income: $71,006
- Total population: 2,564
26. Tesuque, NM (Rocky Mountains)
- Homes worth $1,000,000 or more: 36.0%
- Median household income: $56,250
- Total population: 1,123
25. Tahoe Vista, CA (Sierra Nevada)
- Homes worth $1,000,000 or more: 40.8%
- Median household income: $91,944
- Total population: 1,171
24. Sunnyside-Tahoe City, CA (Sierra Nevada)
- Homes worth $1,000,000 or more: 40.9%
- Median household income: $125,144
- Total population: 1,536
23. Dollar Point, CA (Sierra Nevada)
- Homes worth $1,000,000 or more: 41.3%
- Median household income: $113,269
- Total population: 1,233
22. Edwards, CO (Rocky Mountains)
- Homes worth $1,000,000 or more: 41.4%
- Median household income: $89,399
- Total population: 10,721
21. Emigration Canyon, UT (Wasatch Range)
- Homes worth $1,000,000 or more: 41.7%
- Median household income: $138,125
- Total population: 1,503
20. Jackson, WY (Rocky Mountains)
- Homes worth $1,000,000 or more: 42.4%
- Median household income: $101,477
- Total population: 10,748
19. Vail, CO (Rocky Mountains)
- Homes worth $1,000,000 or more: 42.7%
- Median household income: $96,667
- Total population: 4,833
18. Big Sky, MT (Rocky Mountains)
Homes worth $1,000,000 or more: 42.8%
Median household income: $94,176
Total population: 2,825
17. Genoa, NV (Sierra Nevada)
- Homes worth $1,000,000 or more: 44.7%
- Median household income: $116,250
- Total population: 1,013
16. Sun Valley, ID (Rocky Mountains)
- Homes worth $1,000,000 or more: 45.2%
- Median household income: $67,386
- Total population: 1,383
15. Snyderville, UT (Wasatch Range)
- Homes worth $1,000,000 or more: 47.2%
- Median household income: $135,132
- Total population: 5,730
14. East Basin, UT (Wasatch Range)
- Homes worth $1,000,000 or more: 48.7%
- Median household income: $172,614
- Total population: 3,646
13. Aspen, CO (Rocky Mountains)
- Homes worth $1,000,000 or more: 49.1%
- Median household income: $94,338
- Total population: 6,952
12. Breckenridge, CO (Rocky Mountains)
- Homes worth $1,000,000 or more: 49.1%
- Median household income: $129,481
- Total population: 5,017
11. Summit Park, UT (Wasatch Range)
- Homes worth $1,000,000 or more: 49.6%
- Median household income: $171,408
- Total population: 8,708
10. Wilson, WY (Rocky Mountains)
- Homes worth $1,000,000 or more: 49.7%
- Median household income: $128,981
- Total population: 1,303
9. Crested Butte, CO (Rocky Mountains)
- Homes worth $1,000,000 or more: 50.6%
- Median household income: $67,625
- Total population: 1,434
8. South Park, WY (Rocky Mountains)
- Homes worth $1,000,000 or more: 52.6%
- Median household income: $109,402
- Total population: 1,899
7. Snowmass Village, CO (Rocky Mountains)
- Homes worth $1,000,000 or more: 58.1%
- Median household income: $94,761
- Total population: 3,076
6. Blue River, CO (Rocky Mountains)
- Homes worth $1,000,000 or more: 59.9%
- Median household income: $150,074
- Total population: 1,238
5. Basalt, CO (Rocky Mountains)
- Homes worth $1,000,000 or more: 65.8%
- Median household income: $103,049
- Total population: 3,815
4. Mountain Village, CO (Rocky Mountains)
- Homes worth $1,000,000 or more: 66.7%
- Median household income: $56,917
- Total population: 1,582
3. Park City, UT (Wasatch Range)
- Homes worth $1,000,000 or more: 69.6%
- Median household income: $132,315
- Total population: 8,379
2. Moose Wilson Road, WY (Rocky Mountains)
- Homes worth $1,000,000 or more: 73.6%
- Median household income: $105,673
- Total population: 1,143
1. Silver Summit, UT (Wasatch Range)
- Homes worth $1,000,000 or more: 84.1%
- Median household income: $226,442
- Total population: 1,703